Friday, September 9, 2011
Tips and Tricks for a Valve Inspection on a Suzuki C50
Preparing the bike
1. Put the bike on the bike jack.
2. Raise all the way up
3. Lower the jack's safety rod and lower the bike onto the highest stop point.
4. Secure the bike to to the jack with straps
Things I had to remove from the bike
1. Speedo
2. Seat
3. Tank
4. Both the Left and right side covers
5. Right side neck cover (key cover)
6. Air filter box and snorkel (every thing) - Follow service manual procedure
7. Throttle Body - Completely remove, and let it hang over the frame on the throttle wires. - Follow service manual procedure.
8. Rear cylinder, left side chrome cover
9. Front cylinder, right side chrome cover
10. Both spark plugs
11. Pair valve chrome tube attached to the rear cylinder, 2 small bolts on the rear of the rear cylinders.
12. All the valve covers. This was tricky, I hand to make a trip to Sears to get a Metric Flex socket set because I couldn't figure and other way to remove a few of the cover bolts.
13. Both the crank cover and the flywheel inspection window.
I used the feeler gauge method, and didn't have a problem getting the feeler gauge to get in under the tappets. I had to bend them into a "z" to get them to fit, but that was no big deal. And with the throttle body removed, I had more room to work. I wouldn't think twice about removing the throttle body again. It was easy off and easy on.
Also, I have read that many people here have been having trouble finding top dead center. This confused me too at first, so here is what I have learned.
To find Top dead center you fist have to know which are the exhaust and which are the intake valves. Pretty easy, exhaust valves are near the exhaust pipes, and the intake valves are near the center of the cylinder. So the outer most set of valves on both cylinders are the exhaust valves.
Next you have to know the sequence of the firing cycle. Also easy:
1. Exhaust valves open (valves go down)
2. Exhaust valves close (valves goes up)
3. Intake valves open (intake valves go down)
4. Intake Valves close ( intake valves go up)
As the intake valves are coming up (closing) the cylinder is approaching Top Dead Center.
What the book says, and what everyone has writing on this subject, is that once you see the intake valves coming up look into the flywheel inspection window and turn the engine slowly to look for the RT or the FT mark (depending on which cylinder you are working on). Although this is correct, people have failed to mention that if you start looking as soon as you see the intake valves coming up you still have to crank the engine a good deal to get to the proper mark.
This through me, I guess because I wasn't expecting it to be so long. So I came up with this:
***At the time this was totally original on my part and I was patting myself on the back for coming up with it, but I have since learned it's an old trick, bummer, but it works.***
When the intake valve were starting to close, I took a very long, very thin screwdriver and stuck it into the spark plug whole and felt the top of the piston, (BTW, the top of the piston was pretty black, but I have also learned that's normal) as I cranked the engine toward Top Dead Center I was able to watch the screw driver rise out of the spark plus hole. When the proper mark (either RT or FT) showed up in the window, the screwdriver was all the up, out of the spark plug whole. Thus I have found Top Dead Center on the compression stroke and was able to make my adjustments.
For the adjustments I followed OregonLAN's Guide How to adjust your valves 101 w/ pics that is a Sticky in the Motors, Transmissions & Drives section of the www.VolusiaRiders.com message board. He did a great job, and his work really helped me a great deal, Thank you.
So after I finished the rear cylinders adjustment, I buttoned everything up, because I'm a little anal and I didn't want to forget where things went. I put the valves covers back on, put the new spark plug in, and put the the chrome covers back before moving over to the other side of the bike to start the adjustments on the front cylinder.
MISTAKE.... You can't put either of the sparks plug back until you are finished with the valve adjustments. Why?, because you wont be able to turn the engine over with one the sparks plugs in. The compression air needs needs someplace to go, and it goes out the spake plug hole.
I didn't realize that, live and learn, and now maybe the next member here will.
My adjustment turned out just fine, no problems, but it took me all afternoon, about 5 hours. I think next time it will go much quicker now that i know what to expect. I hope others who sit through this post can learn from some of my mistakes, benefit from some of my experiences, and realize that this necessary maintenance procedure is very doable by anybody.
Thanks for reading, James.
Friday, June 17, 2011
Helmet Lock
When I installed my saddlebags the OEM helmet lock got covered up, so I had to relocate it. I installed it behind the vertical license plate. You use the bottom license plate mounting hole then mark the license plate backing plate where the helmet lock stud touches. Drill out the backing plate to the right size and mount the lock. Easy no money mod for those with saddle bags.
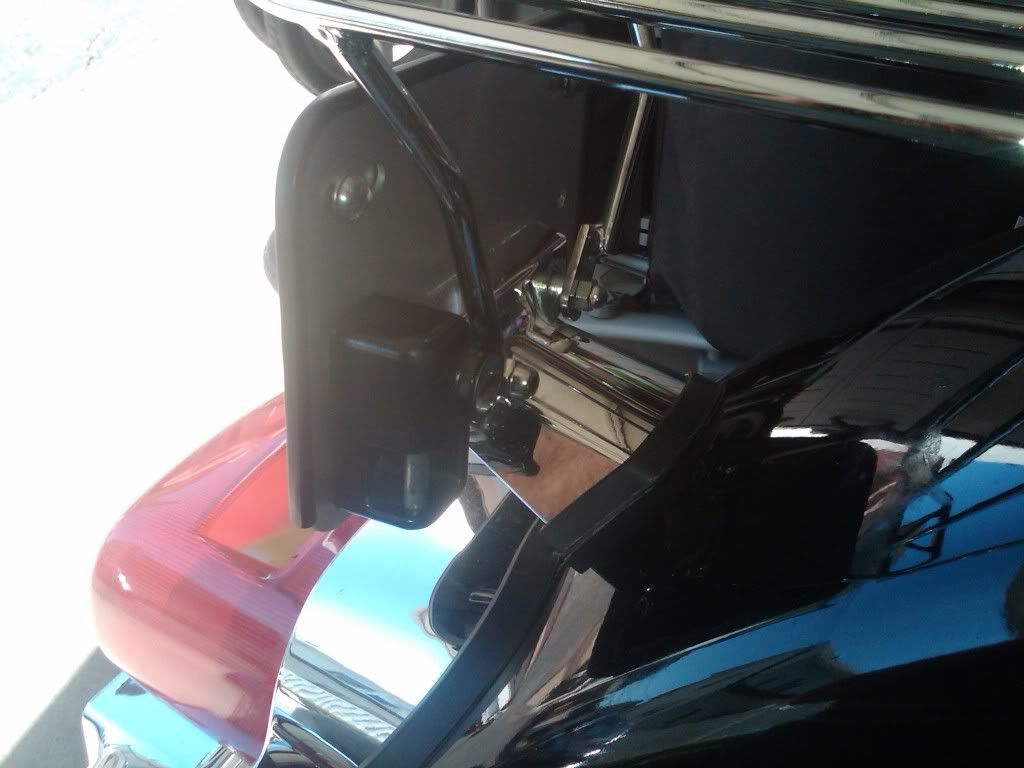
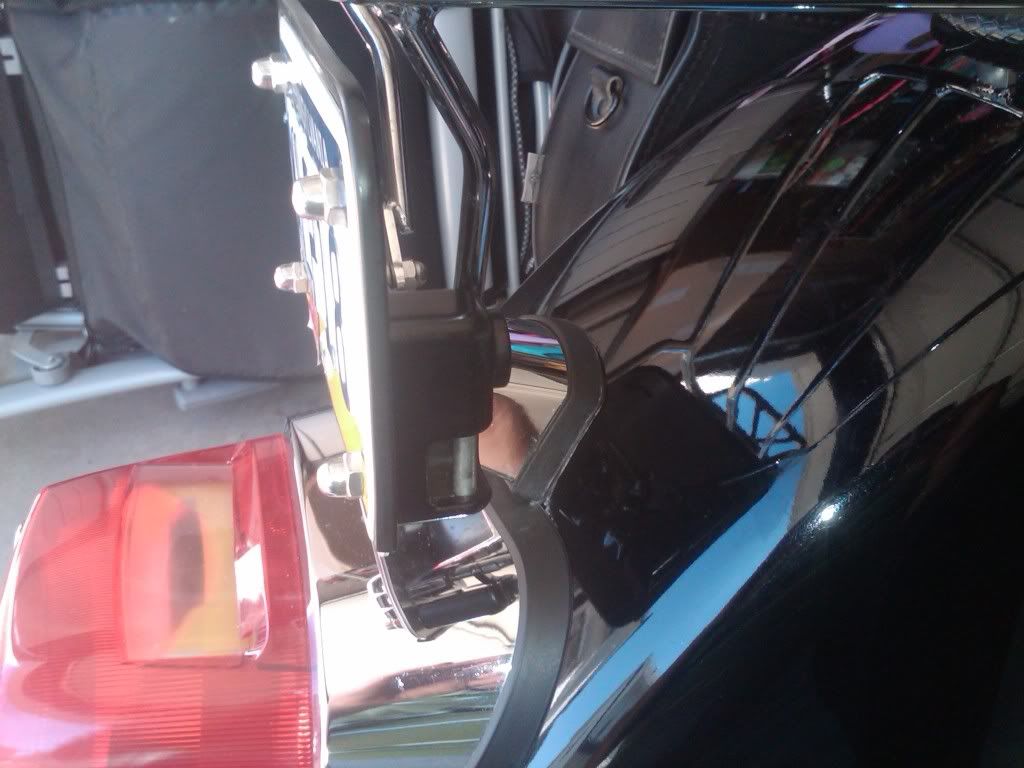
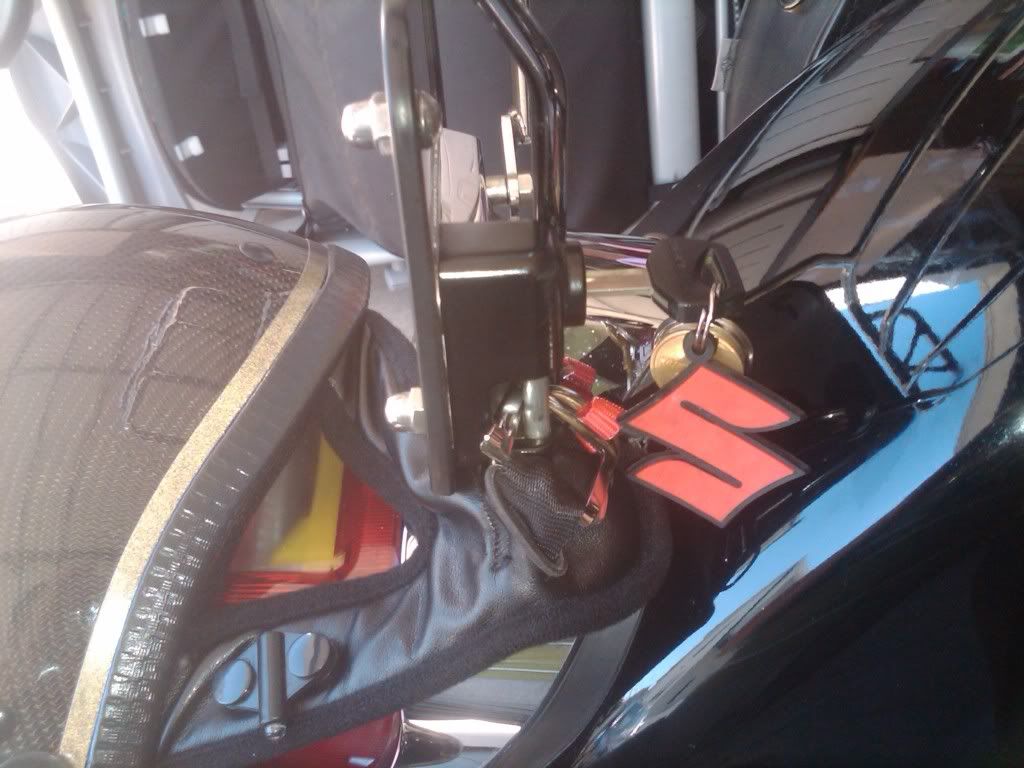
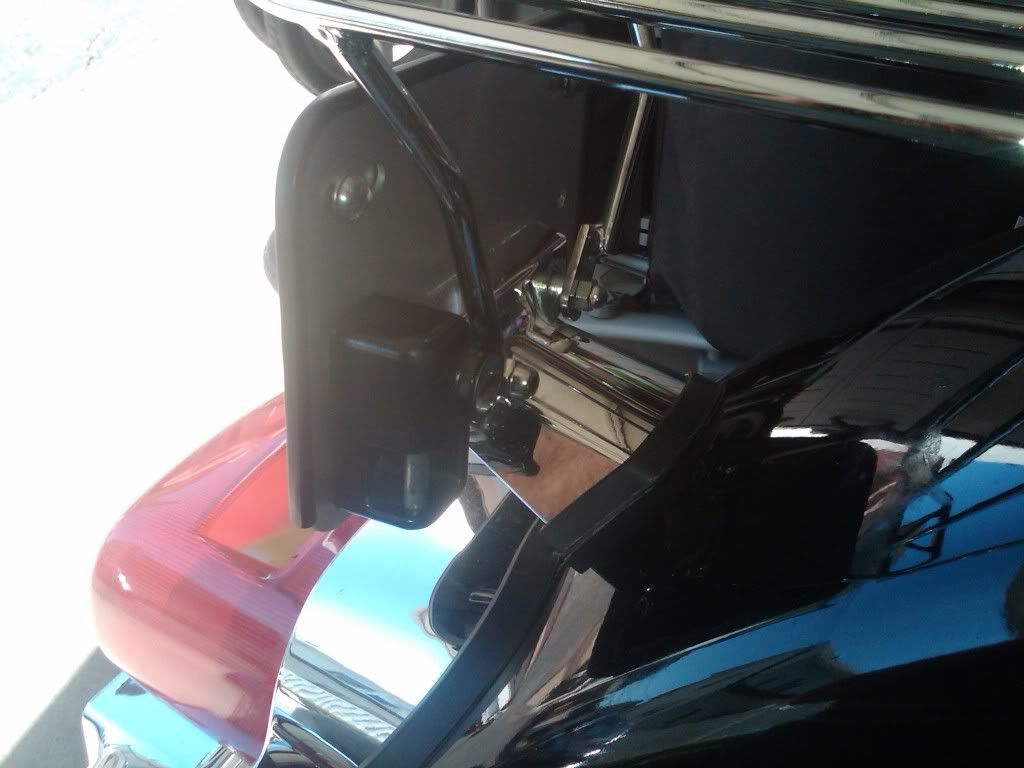
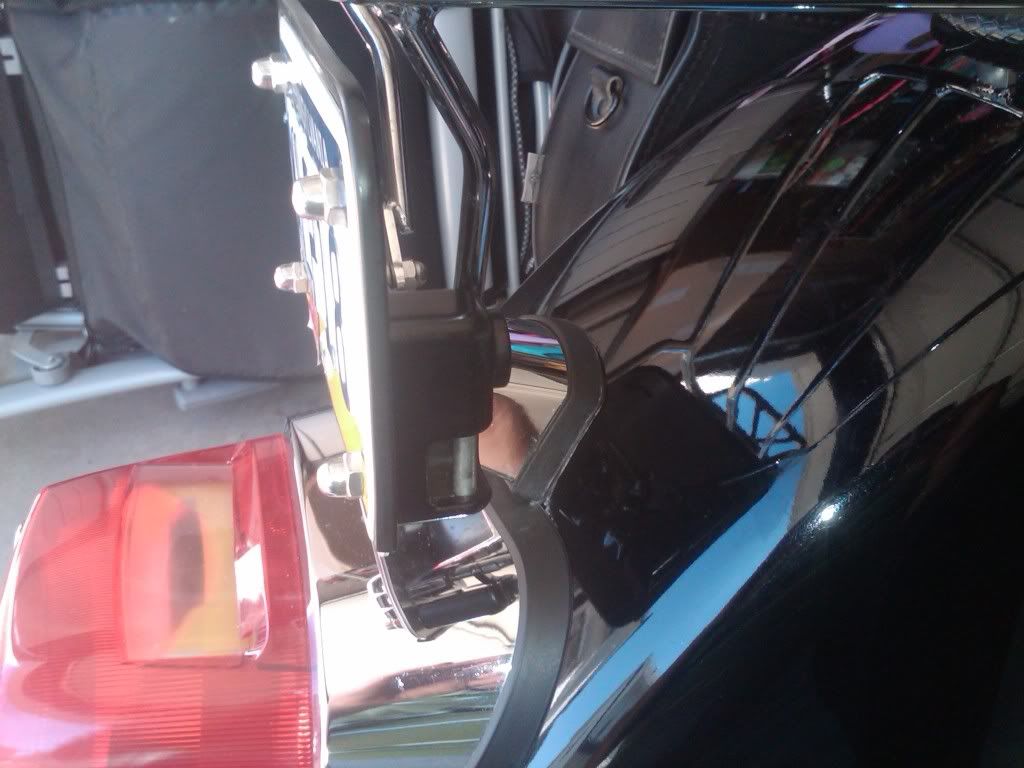
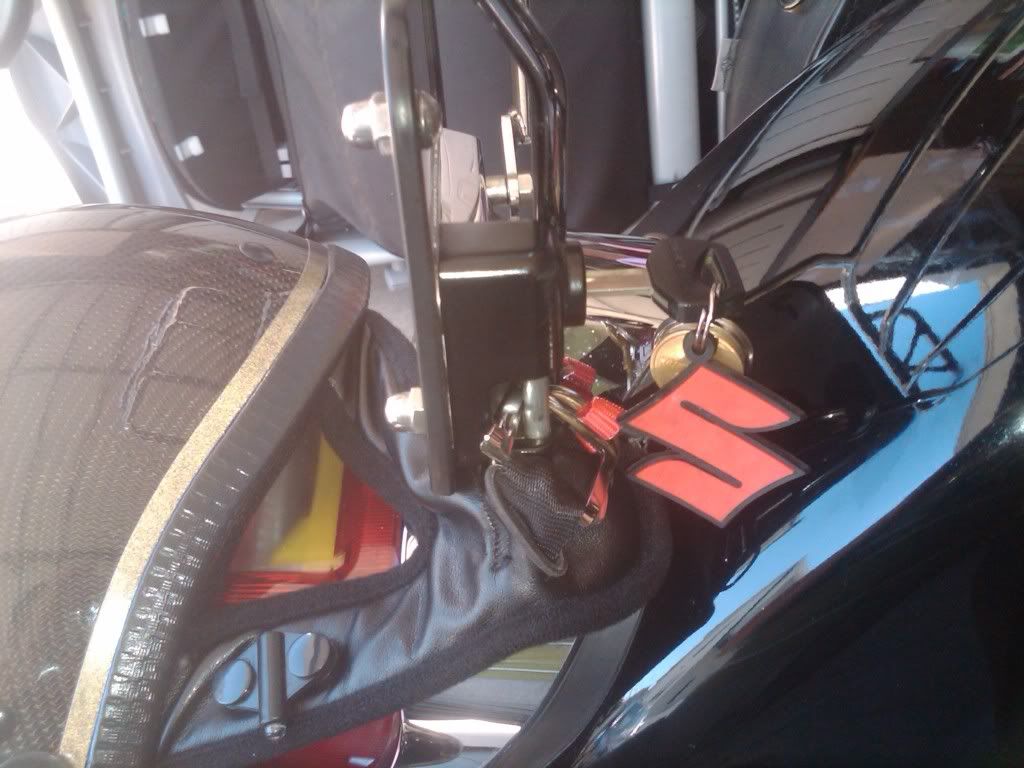
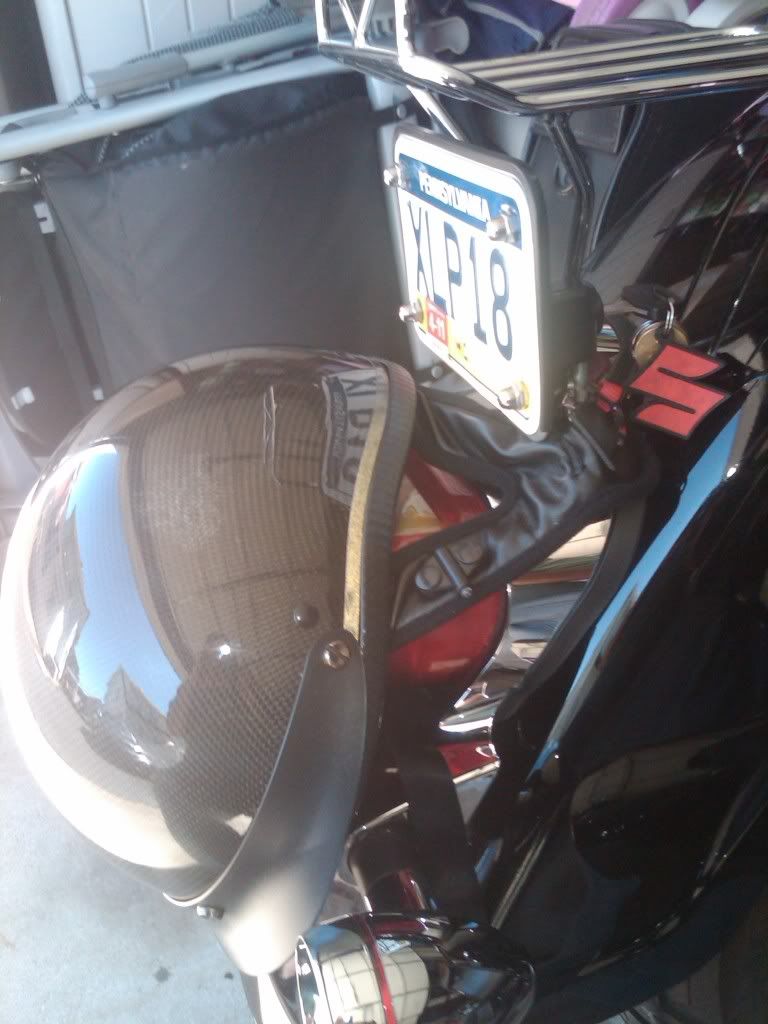
4" Risers
I installed these SWITCHBACK CHROME 4" HANDLEBAR RISERS . They are little bit different from the ones that I see all the time. The chrome seems solid. My only complaint so far is that they didn't come with mounting bolts, and since they are for Harley's they aren't metric. A quick trip the Home Depot to get some hardened steel 1/2" bolts solved this.
Here are come pictures:
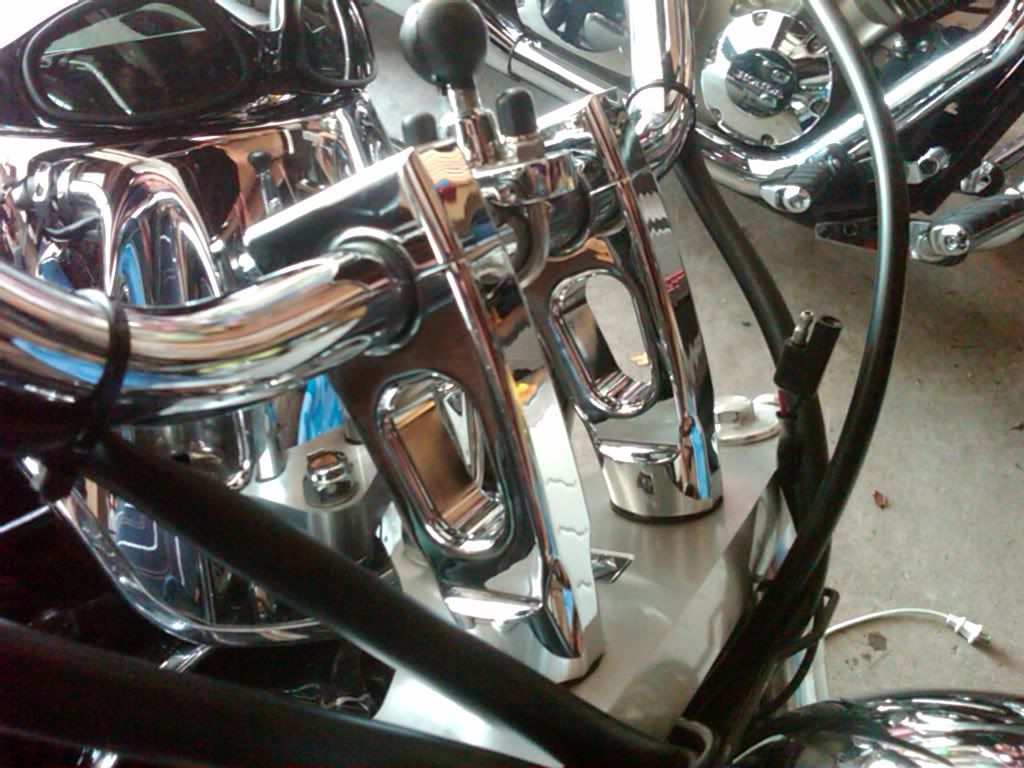
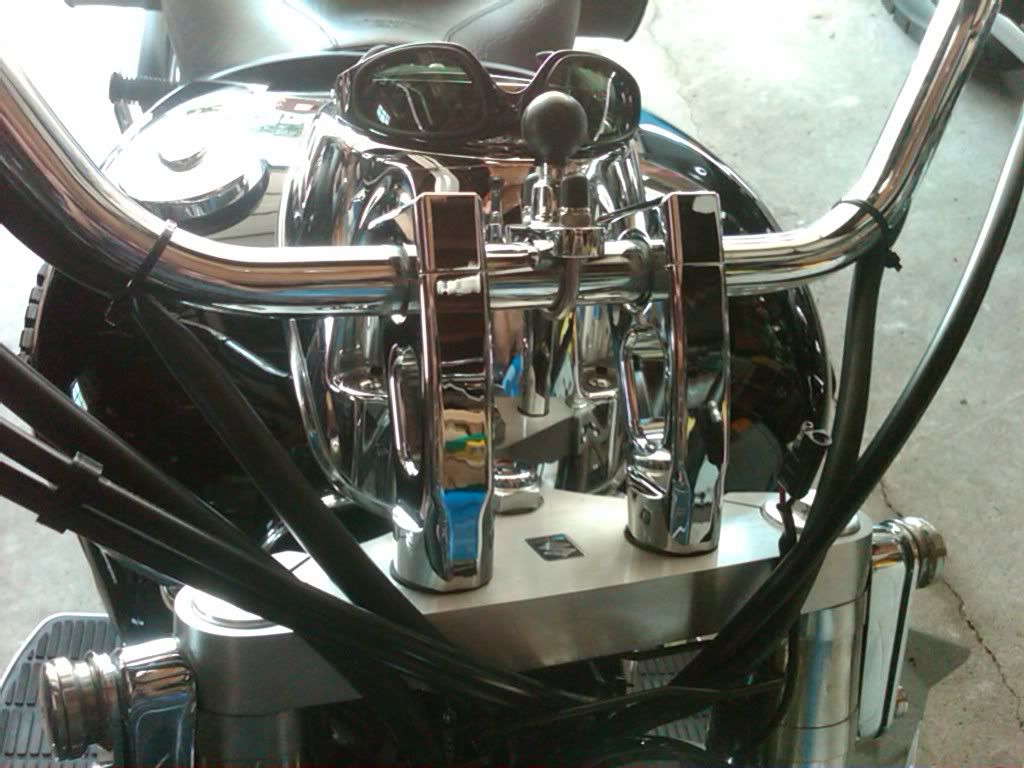
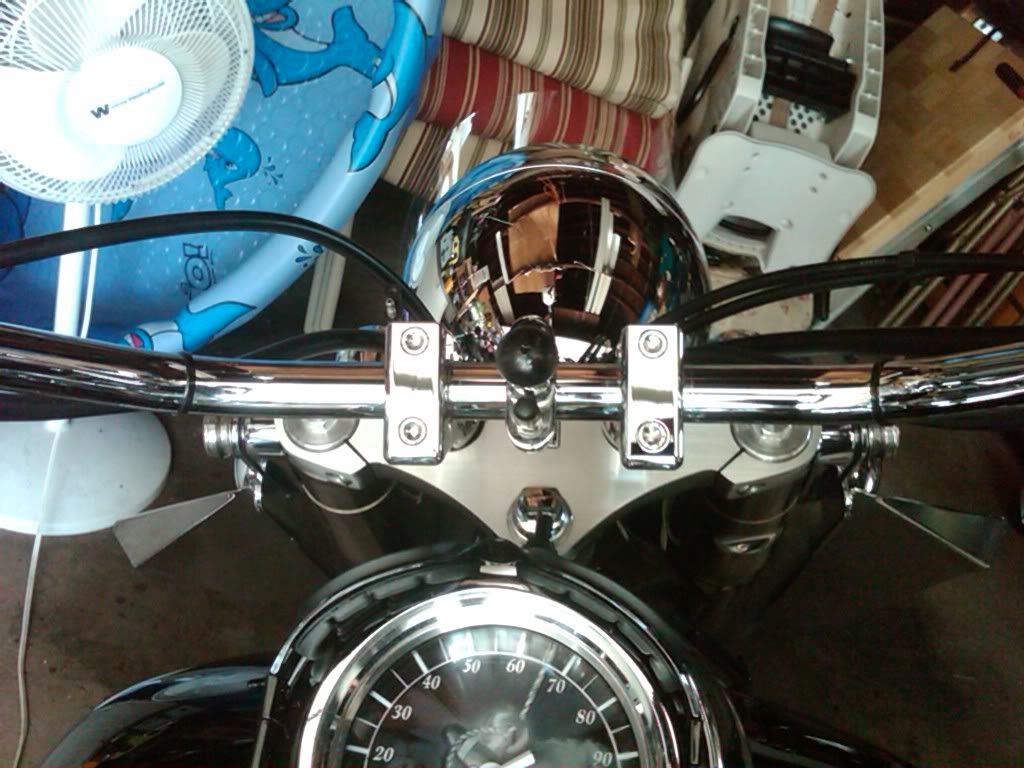
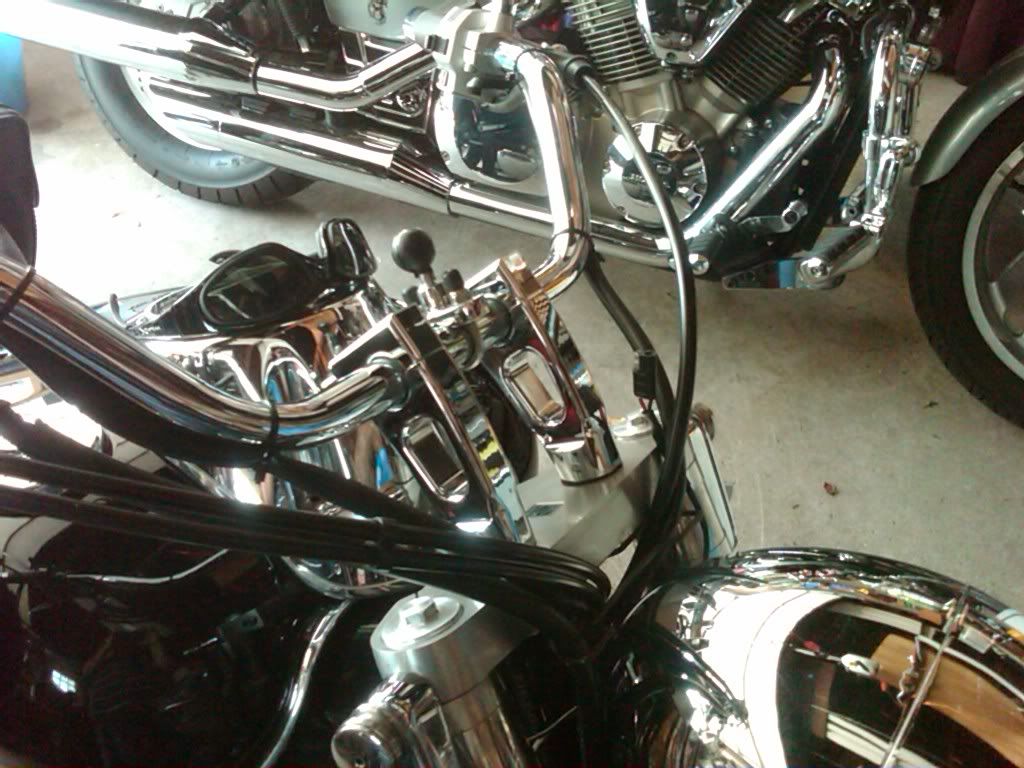
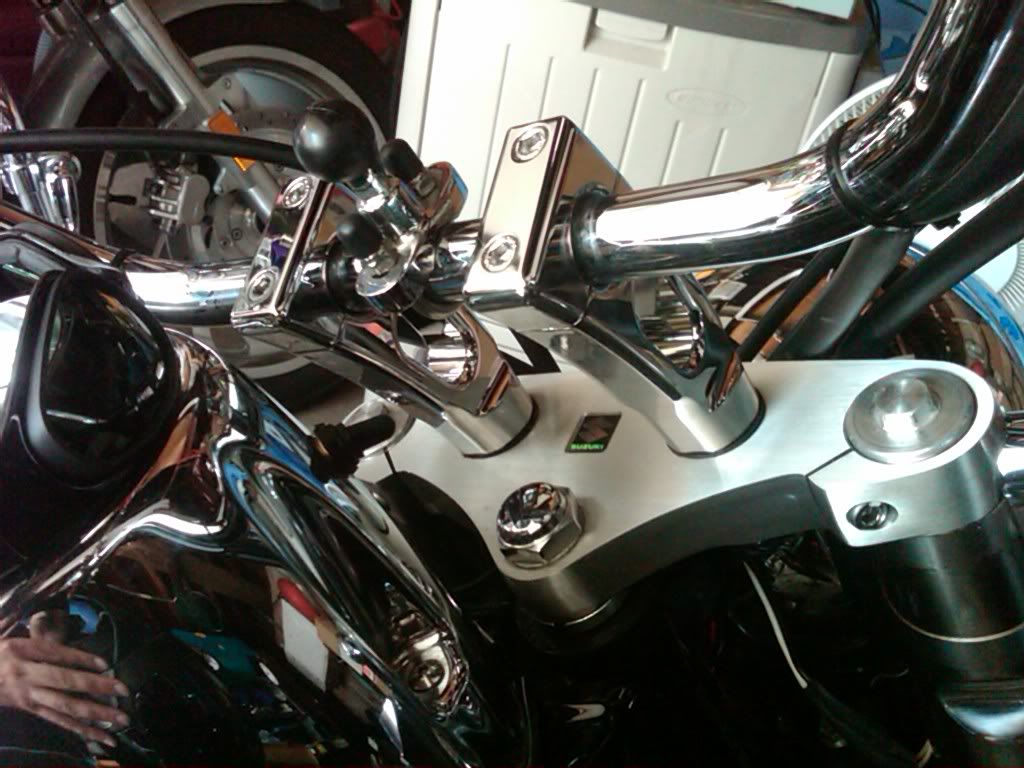
I know, a lot of pictures for just risers, but if any of you out there are like me, then you would like to see the product on the bike before you make a purchase.
James
Here are come pictures:
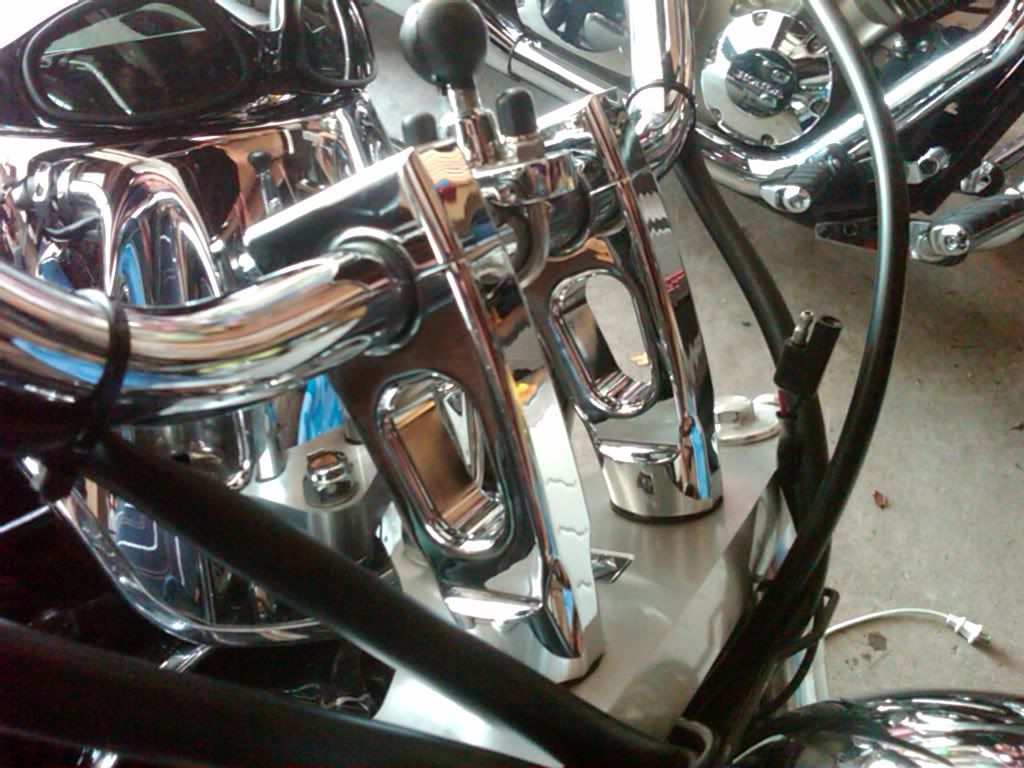
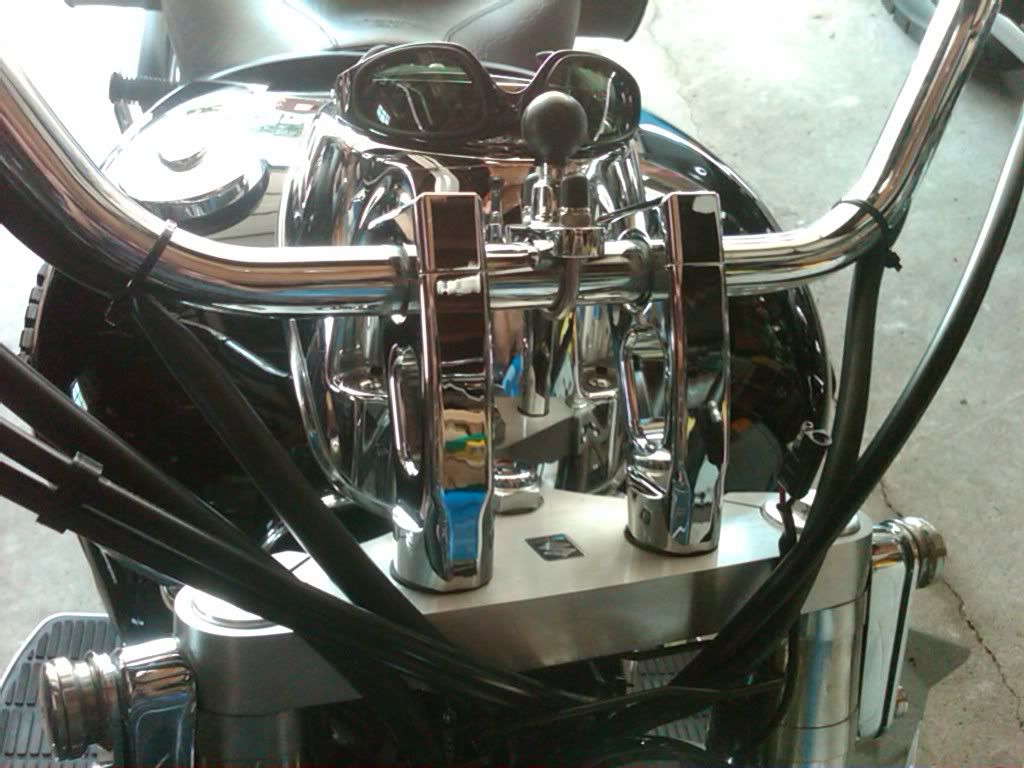
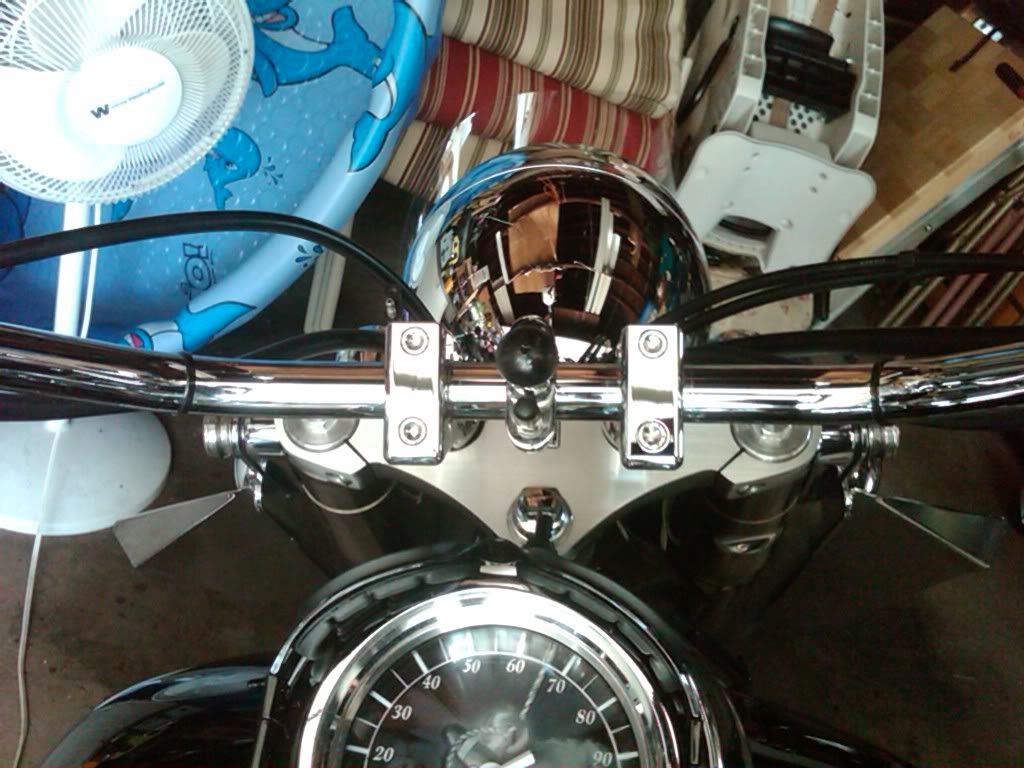
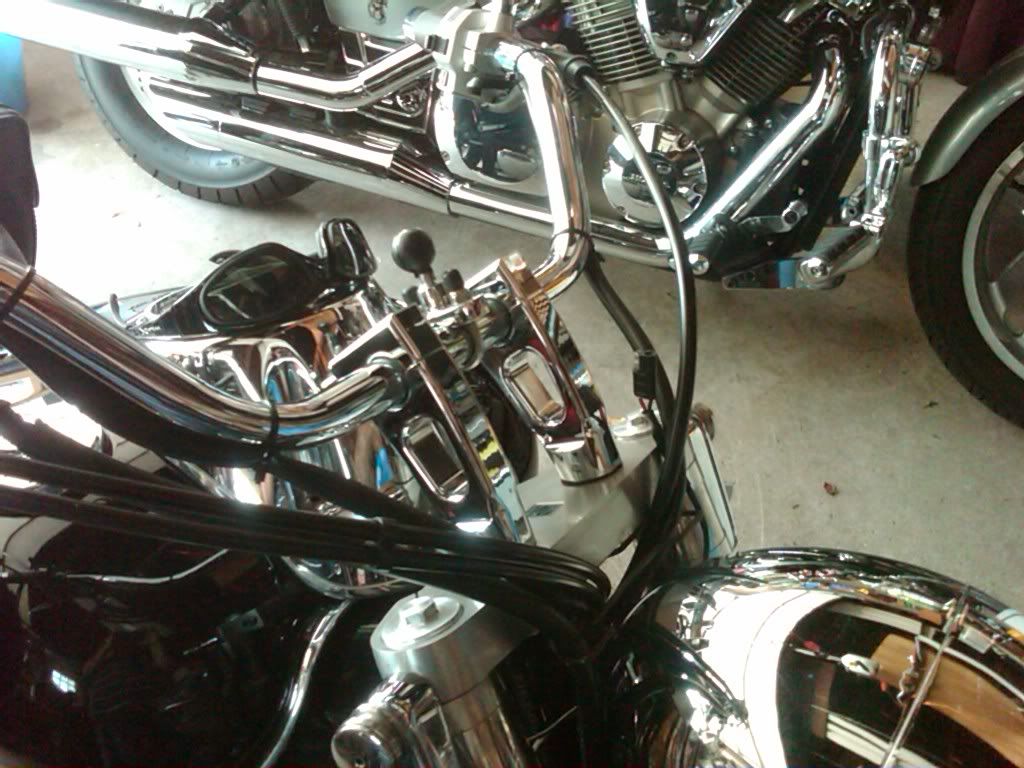
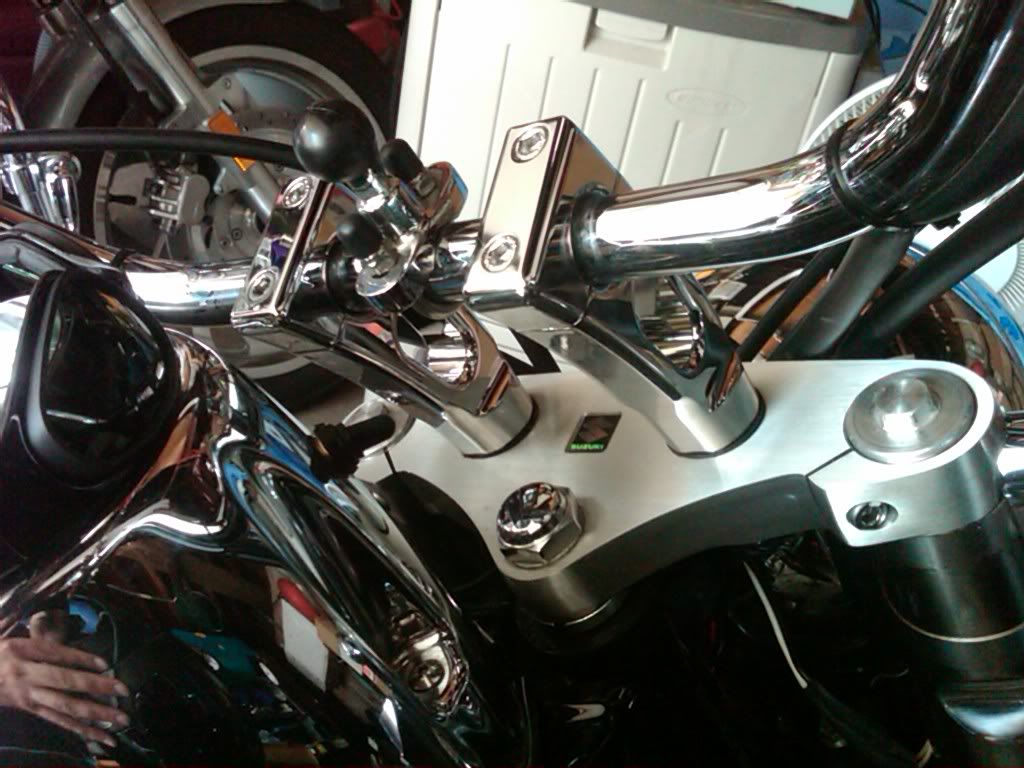
I know, a lot of pictures for just risers, but if any of you out there are like me, then you would like to see the product on the bike before you make a purchase.
James
Wal-Mart Lights Install
This is an old blog that I am re-writing for anyone who is looking to do this install. I have since gone on to using a Kuryakyn light bar. There is a lot of relevant information in this post, especially the part of using a relay to power accessory lights. So here is an oldie but a goodie...
In an effort to keep things simple for anyone who wants to install these lights I wrote up a procedure that works, with pictures, lots of pictures, and it is wired so the lights turn off when you start the bike just like the headlight.
What you will need:
Pilot Motorsports: Wiring Harness w/Switch part PL-HARN3 from Pep Boys--- you will be cutting this harness up…
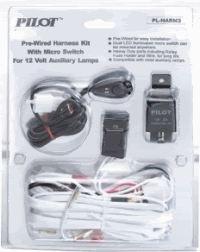
1 spool of 12 gauge red wire and 1 spool of 12 gauge black wire from radio shack
Black wire ties from Wal-Mart
A couple of packages of heat shrink from Wal-Mart
2 “eye-type” terminal connectors to connect red and black wire to the battery - got it in a package from Wal-Mart
Wal-Mart Driving Lights
If you choose to install a switch here are some choices for a 12v switch …(tip: nothing from radio shack, nothing they make is exterior grade) –
Here are some choices:
1. Order a handlebar mounted 12v switch online
2. Go to a marine supply store and get a 12 volt toggle switch
3. Go to local motorcycle shop and see what they have
4. Try these choices from Allied Electronics www.alliedelec.com
A quality 12 toggle switch: http://tinyurl.com/5wk27c
But more importantly use at toggle switch boot to cover the outside of the switch, this will make it water tight: http://tinyurl.com/658p4u
My brother used a handlebar mounted 12v switch and took it all apart to the guts of the switch then mounted it into my speedo housing.
A roll of Plastic Wire Cover from Wal-Mart
Soldering iron and solder….I use small silver solder from Radio Shack
Instructions:
First off prepare the Wal-Mart lights…
What I did was take two small diameter pieces of heat shrink and put one piece on each end of the wire coming out of the end of the Wal-Mart lights. Then I put a larger piece of heat shrink over the two and really jammed it into the back of the light housing, this made a pretty good weather seal, you can also use some high heat silicone or gasket silicone but I didn’t think I would be able to do that neat enough. Also, others have rightly suggested installing a small set screw on the bottom portion of the lip that holds the lens in place. This is a great idea and should be done. Just drill a small hole in the bottom of the lens bevel and install an equally sized (smallest you can find) stainless steel screw with some blue lock-tight, so the lens wont vibrate off.
Mounting the Wal-Mart lights…
Before you even begin tearing into the bike you can test mount, then mount the lights. Mount them as far as possible to the edge of the turn signal trim piece. Just leave yourself enough of room underneath to get your nut and washer in there. It’s ok to let the mount overhang the side of the trim. When you drill the hole for the bolts in the trim piece use a small bit at first drilling from the outside, then work up to correct size drilled hole. (Hint…please use rubber washers between the plastic trim piece and the mount on both sides, you can over tighten the mounting nut and crack the plastic trim, I know from experience) Remember to use blue lock-tight on all the mounting nuts and do not over tighten.
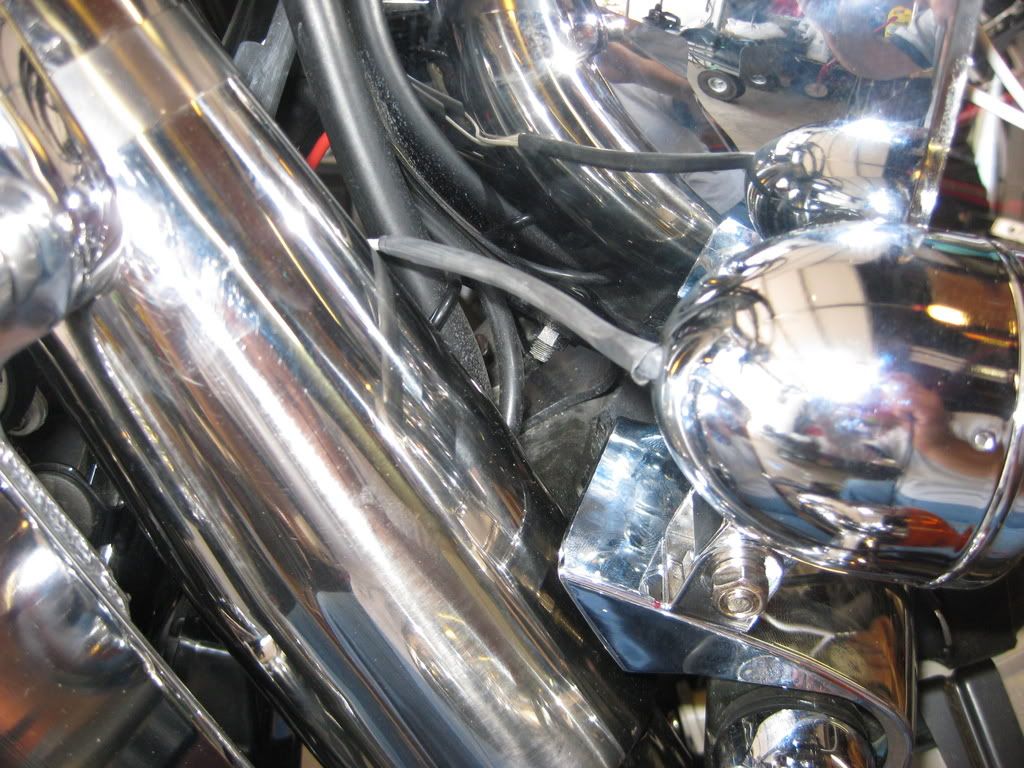
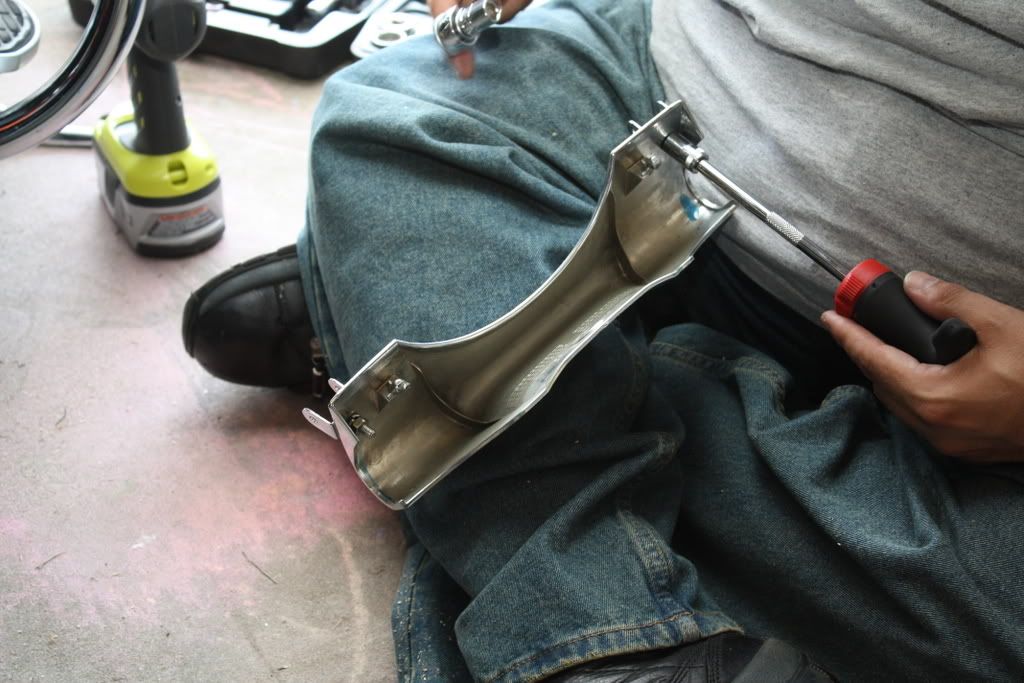

In the wiring harness that came with the Wal-Mart Lights find the lengths of wire that connects to the lights and cut them a few feet back from the connectors. Slide some large heat shrink over it and connect the plug connectors from the lights to the shot of wire. Next slide the heat shrink over the plug connectors and heat em’ up. (tip: I did not solder these connectors so if I want to replace the 15 dollar lights with something better someday it will be an easy job, but feel free to cut the connectors away and solder in the wire directly to the lights if you want) Now, route the wire up into the headlight bucket.
After I mounted the lights I moved on to pulling the power from the Battery….
Now is a good time to stop and talk about your connections…all of the connections that you will make should be soldered then heat shrunk (I use sliver solder from Radio Shack because it keeps the Vampires away, and it melts fast)…remember to slip on the right size heat shrink before you splice and solder.
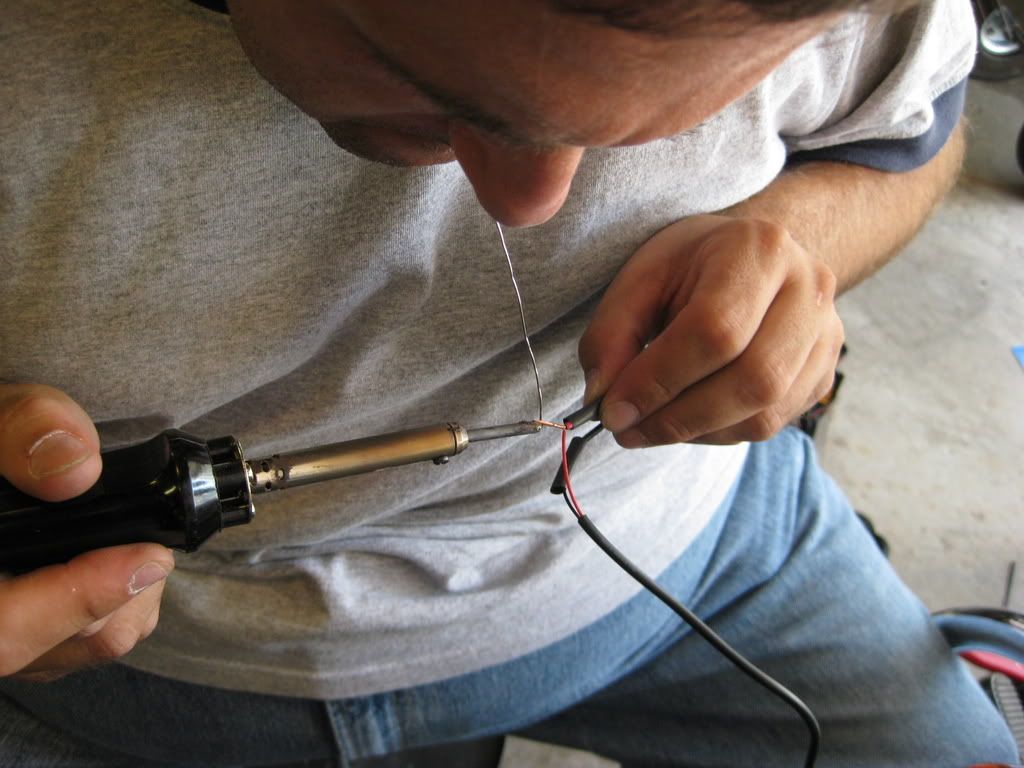
Remove the seats to expose the battery. Also, I removed the tank. Some people grimace about removing the tank but I find it easy and once you have the seats off it really only takes another minute to remove. First unscrew the bolt holding it down, prop it up with a piece of 2x4 or something (I just have someone hold it) then disconnect the wiring harness and unsnap the fuel line. The tank can now be lifted off.
Disconnect the battery cables so the bike is truly dead. (tip: place something like a short piece of spare 12 gauge wire under the nut on the battery terminal…this will help you get the screw back on later)
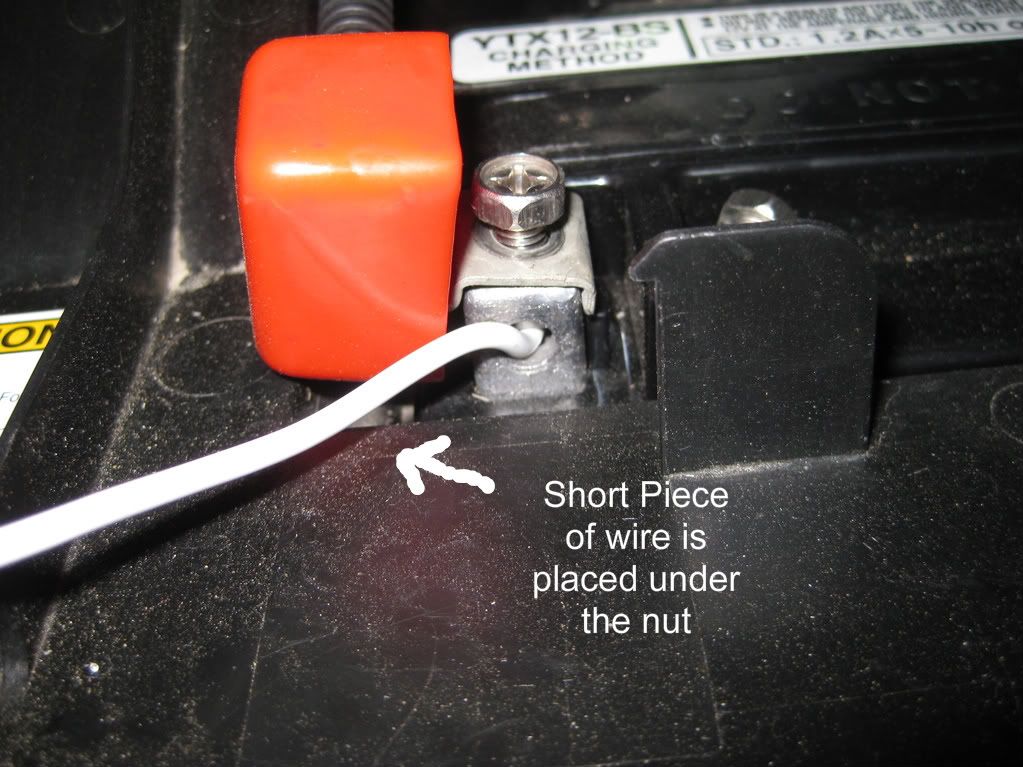
Take the in-line fuse that came with the driving lights and cut it off its wire leaving a few inches to either side. Then solder and heat shrink in about 10 inches of the red radio shack 12 gauge wire to one side of the fuse and about 5 ft of the red radio shack wire to the other side.
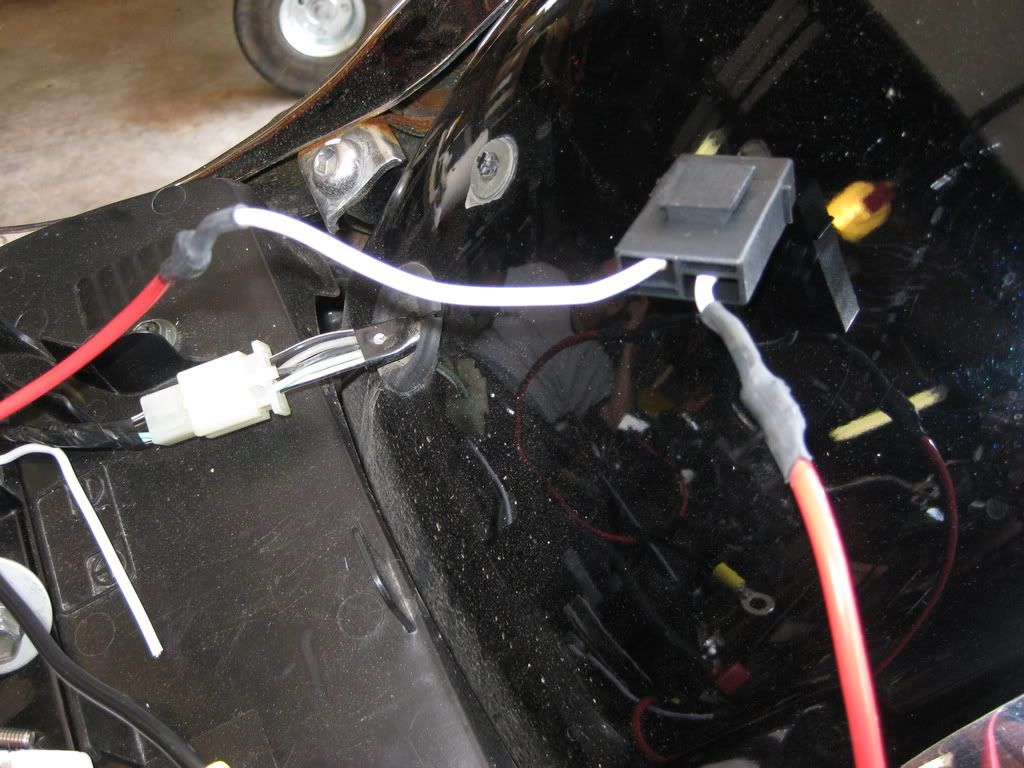
Next at the end of the 10” side Crimp then solder on a Battery connector.
Next take about 5 ft of the black wire and on one end crimp then solder another battery cable.
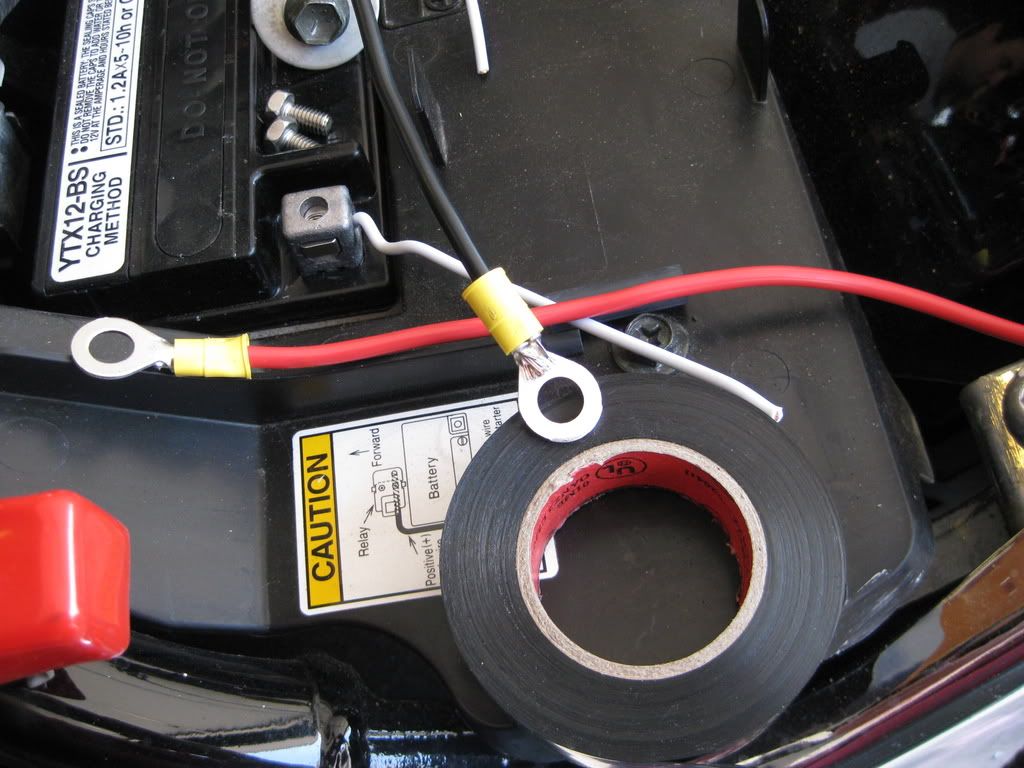
Do Not connect to the battery at this time….that will be the last thing that you do.
Your going to bind the red and black wires together every few inches with electrical tape and run it into the headlight bucket leaving enough of slack make all you connections. Secure the wires every few inches with wire ties where ever you see fit to secure it.
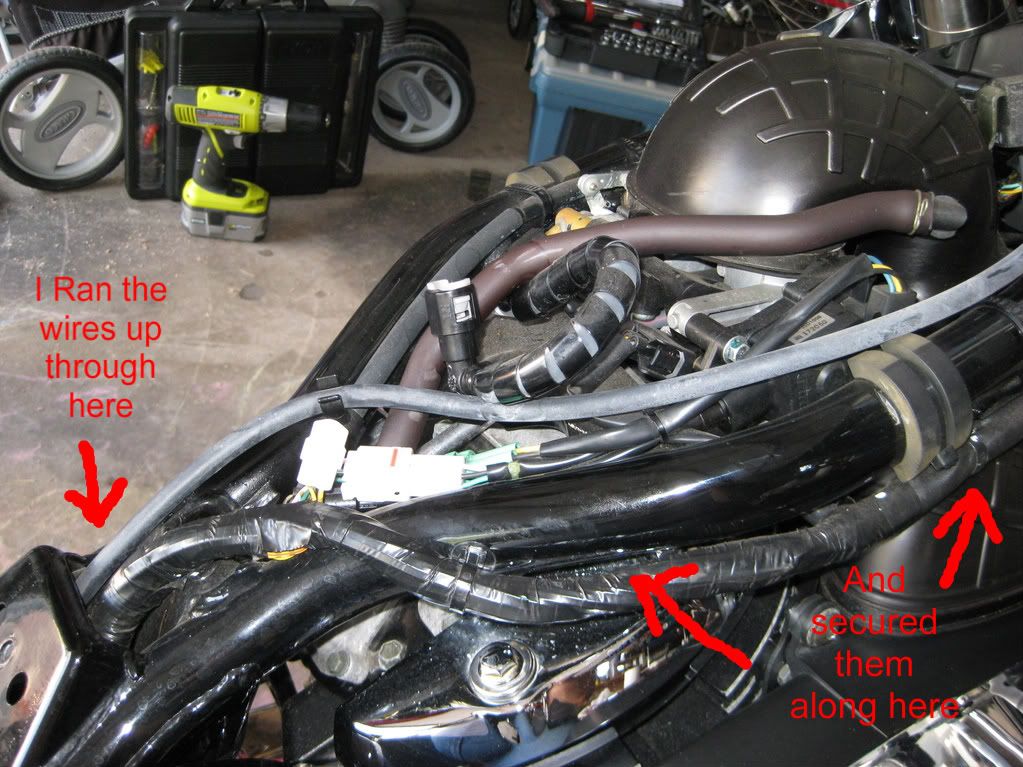

Then you can secure the tank back to the frame.
Open the Headlight Bucket.
Open the Pilot Relay Wiring Harness from the auto store. (if you don’t have this harness you can still follow this procedure by following the diagram below, the harness just makes it a little easier by making a plug for the relay)
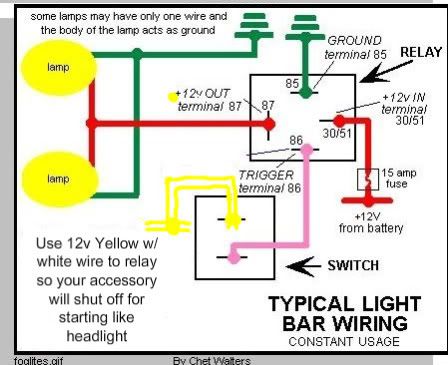
Locate the Yellow wiring harness in the headlight bucket and in that harness there is a yellow with white tracer wire that runs from the harness up the left side of the handlebar into the headlight switch. This wire will be the trigger wire for the relay. I chose to cut this wire and splice in the thin white from the PILOT RELAY WIRING HARNESS remembering to solder and heat shrink the connection. This is the wire that will go to your switch, (I don’t have a switch yet so for me this wire goes right to the relay harness) whether you put it into the speedo housing, or on the neck, or mounted on the handlebars. Now from the switch you will run another piece of 16 gauge wire to the trigger terminal on the relay housing which happens to be the thin white wire coming from the housing. If you are using a switch please either use spade terminals to connect to the switch or install a plug so that in the future you can completely remove the speedo housing.
If you are installing a switch into the speedo housing use a good quality switch like the one from Allied with an external rubber boot cover to keep it watertight. You can also use some Diaelectric compound on the inside terminals to further protect it, but that’s probably over kill.
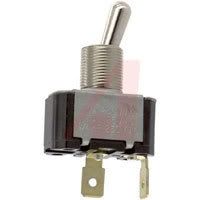
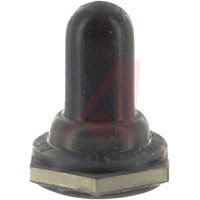
Also from the new relay housing are 2 larger gauge double white wires. These are the wires that will go to your lights. Connect the white wire from each light to the double white wire off of the relay housing in one soldered and heat shrunk connection. (tip: twist the white wire from each light together and then twist the two white wires from the relay housing together, and then twist the four wires together to form one large splice)
Connect our red wire from the battery to the large single white wire off from relay housing remembering to solder and heat shrink. This large white wire is the 12v in wire.
Connect the four remaining black wires together in a large soldered heat shrunk splice. The four black wires are: 1 each from the lights, the black main wire from the battery, and the ground wire from the relay housing.
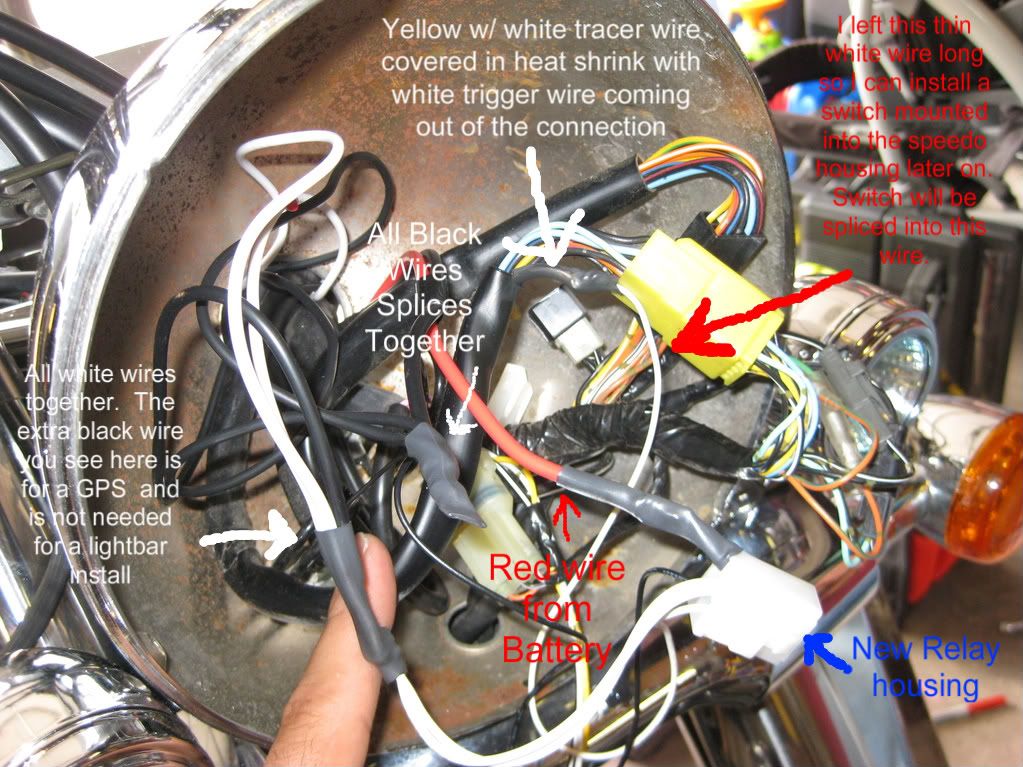
Now place all the wires neatly into the headlight bucket and affix the relay to the relay housing.
Clean up all of your exposed wires with the plastic wire cover.
Connect your Red and Black wires to the battery. (tip: remember to remove the little shots of wire holding up the battery nut) and your going to have to notch the flimsy red plastic casing that covers the red terminal to accommodate the new red wire. YOUR DONE!!!!
Now you are ready to test and button up everything.
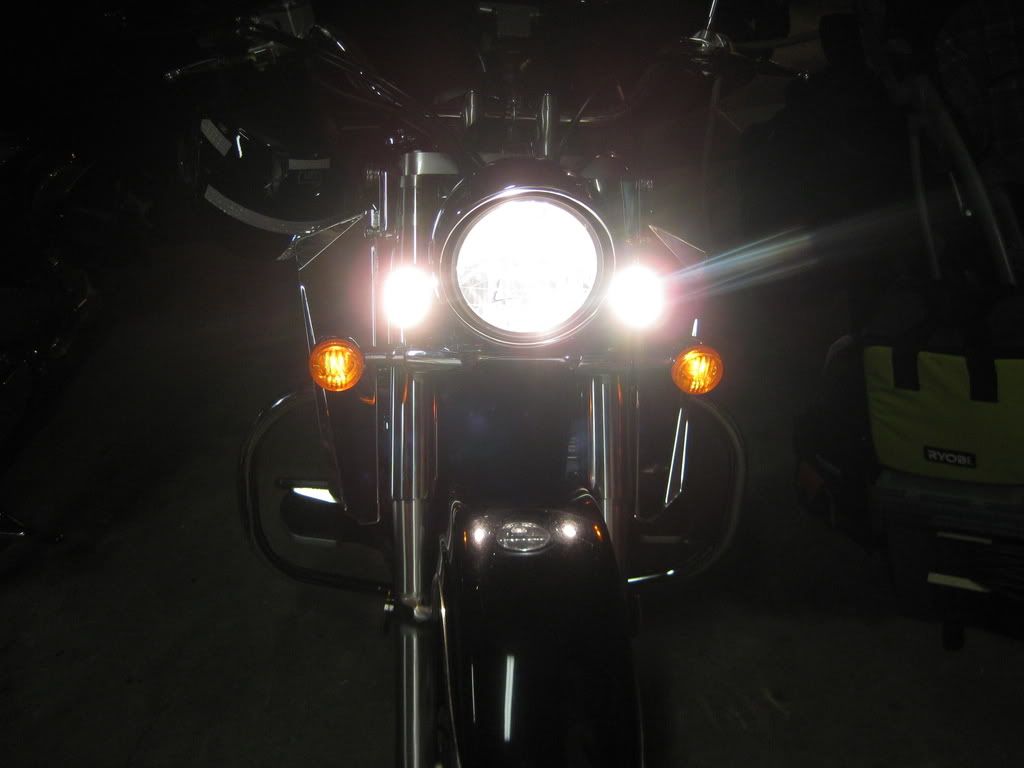
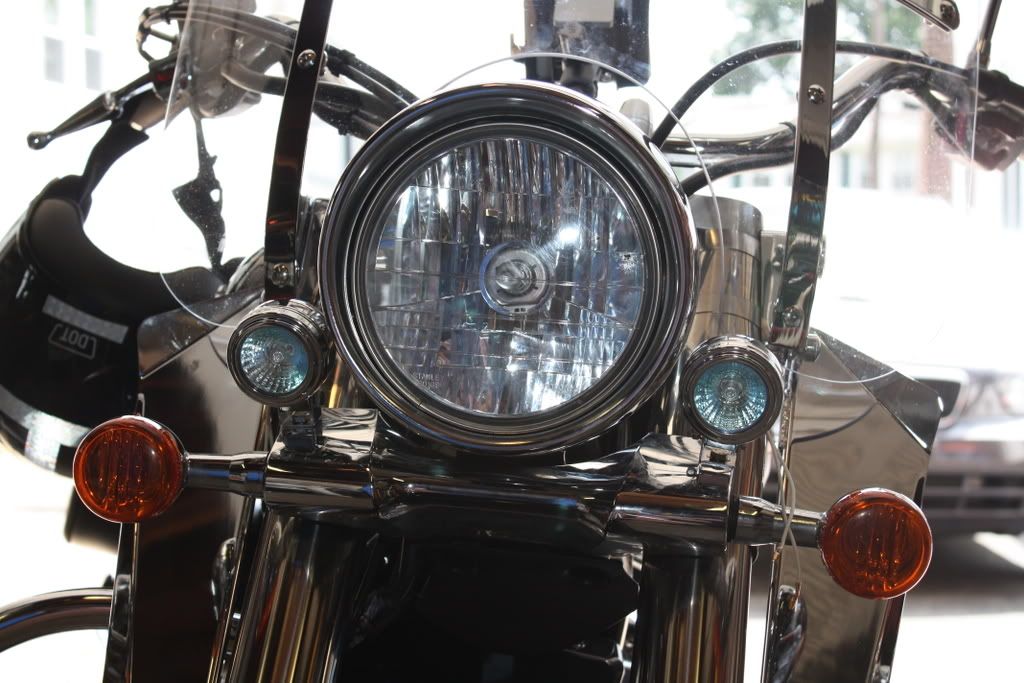
Good Luck!!!
James
__________________
What you will need:
Pilot Motorsports: Wiring Harness w/Switch part PL-HARN3 from Pep Boys--- you will be cutting this harness up…
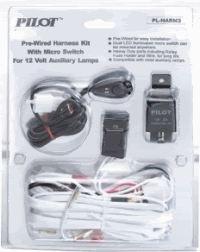
1 spool of 12 gauge red wire and 1 spool of 12 gauge black wire from radio shack
Black wire ties from Wal-Mart
A couple of packages of heat shrink from Wal-Mart
2 “eye-type” terminal connectors to connect red and black wire to the battery - got it in a package from Wal-Mart
Wal-Mart Driving Lights
If you choose to install a switch here are some choices for a 12v switch …(tip: nothing from radio shack, nothing they make is exterior grade) –
Here are some choices:
1. Order a handlebar mounted 12v switch online
2. Go to a marine supply store and get a 12 volt toggle switch
3. Go to local motorcycle shop and see what they have
4. Try these choices from Allied Electronics www.alliedelec.com
A quality 12 toggle switch: http://tinyurl.com/5wk27c
But more importantly use at toggle switch boot to cover the outside of the switch, this will make it water tight: http://tinyurl.com/658p4u
My brother used a handlebar mounted 12v switch and took it all apart to the guts of the switch then mounted it into my speedo housing.
A roll of Plastic Wire Cover from Wal-Mart
Soldering iron and solder….I use small silver solder from Radio Shack
Instructions:
First off prepare the Wal-Mart lights…
What I did was take two small diameter pieces of heat shrink and put one piece on each end of the wire coming out of the end of the Wal-Mart lights. Then I put a larger piece of heat shrink over the two and really jammed it into the back of the light housing, this made a pretty good weather seal, you can also use some high heat silicone or gasket silicone but I didn’t think I would be able to do that neat enough. Also, others have rightly suggested installing a small set screw on the bottom portion of the lip that holds the lens in place. This is a great idea and should be done. Just drill a small hole in the bottom of the lens bevel and install an equally sized (smallest you can find) stainless steel screw with some blue lock-tight, so the lens wont vibrate off.
Mounting the Wal-Mart lights…
Before you even begin tearing into the bike you can test mount, then mount the lights. Mount them as far as possible to the edge of the turn signal trim piece. Just leave yourself enough of room underneath to get your nut and washer in there. It’s ok to let the mount overhang the side of the trim. When you drill the hole for the bolts in the trim piece use a small bit at first drilling from the outside, then work up to correct size drilled hole. (Hint…please use rubber washers between the plastic trim piece and the mount on both sides, you can over tighten the mounting nut and crack the plastic trim, I know from experience) Remember to use blue lock-tight on all the mounting nuts and do not over tighten.
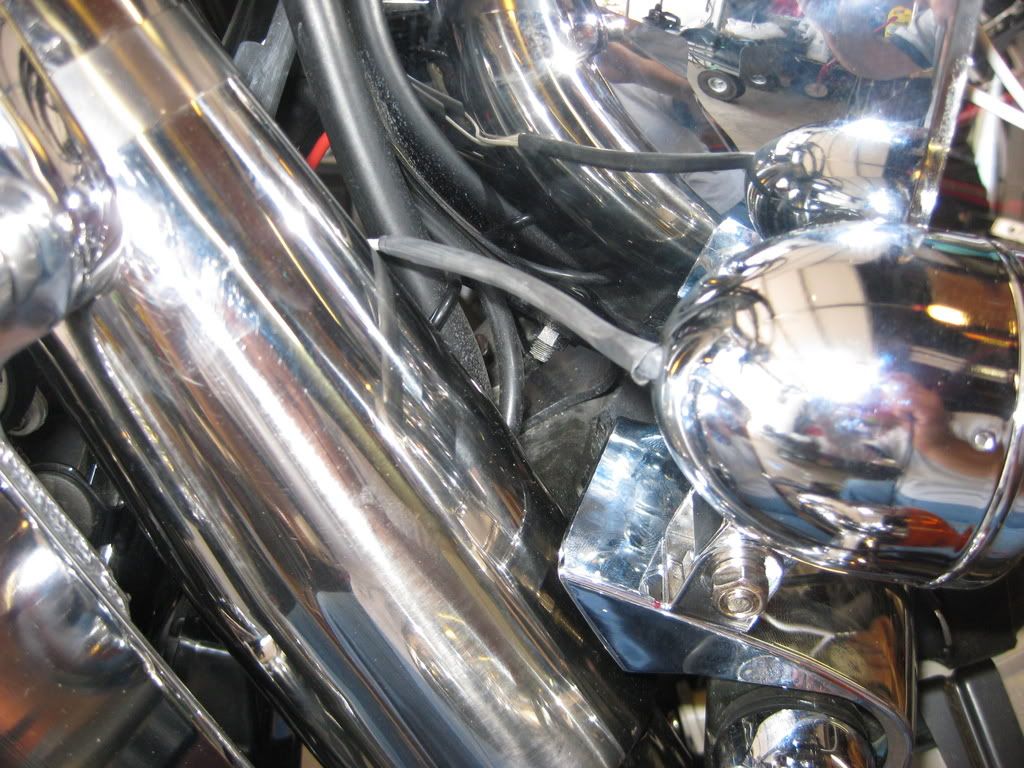
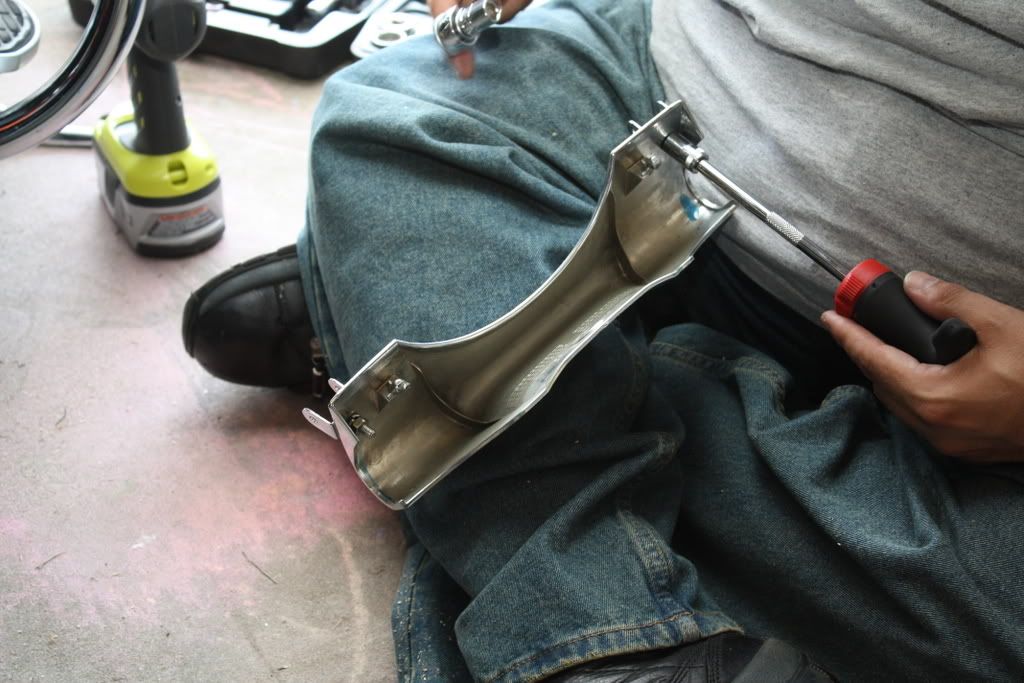

In the wiring harness that came with the Wal-Mart Lights find the lengths of wire that connects to the lights and cut them a few feet back from the connectors. Slide some large heat shrink over it and connect the plug connectors from the lights to the shot of wire. Next slide the heat shrink over the plug connectors and heat em’ up. (tip: I did not solder these connectors so if I want to replace the 15 dollar lights with something better someday it will be an easy job, but feel free to cut the connectors away and solder in the wire directly to the lights if you want) Now, route the wire up into the headlight bucket.
After I mounted the lights I moved on to pulling the power from the Battery….
Now is a good time to stop and talk about your connections…all of the connections that you will make should be soldered then heat shrunk (I use sliver solder from Radio Shack because it keeps the Vampires away, and it melts fast)…remember to slip on the right size heat shrink before you splice and solder.
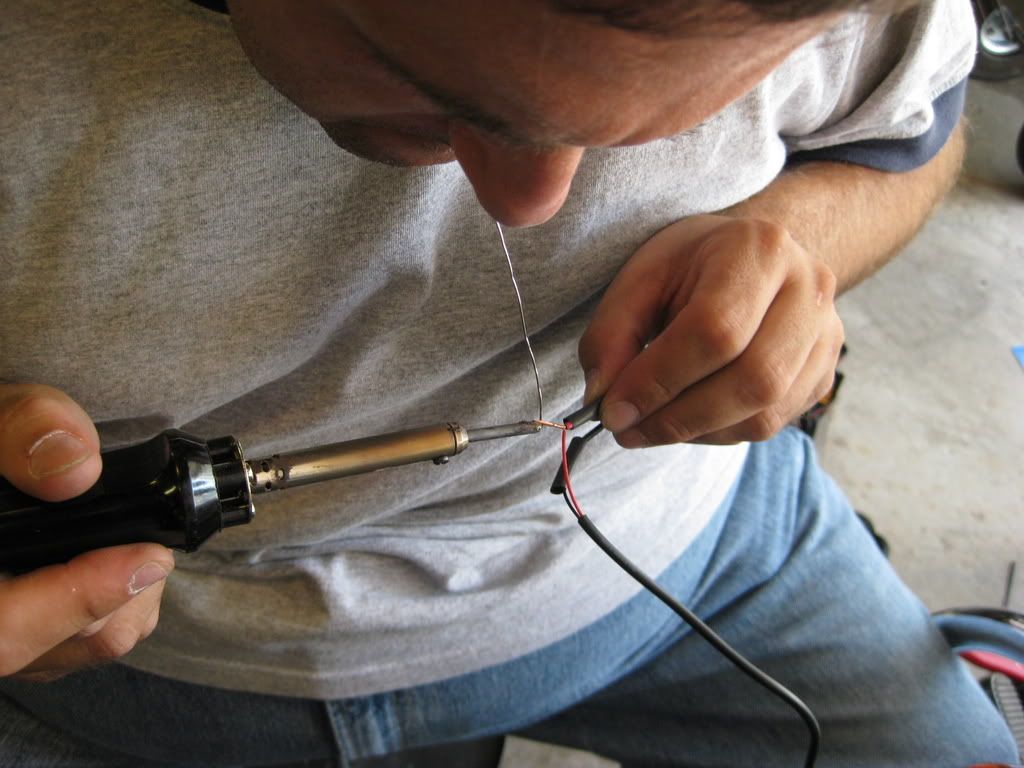
Remove the seats to expose the battery. Also, I removed the tank. Some people grimace about removing the tank but I find it easy and once you have the seats off it really only takes another minute to remove. First unscrew the bolt holding it down, prop it up with a piece of 2x4 or something (I just have someone hold it) then disconnect the wiring harness and unsnap the fuel line. The tank can now be lifted off.
Disconnect the battery cables so the bike is truly dead. (tip: place something like a short piece of spare 12 gauge wire under the nut on the battery terminal…this will help you get the screw back on later)
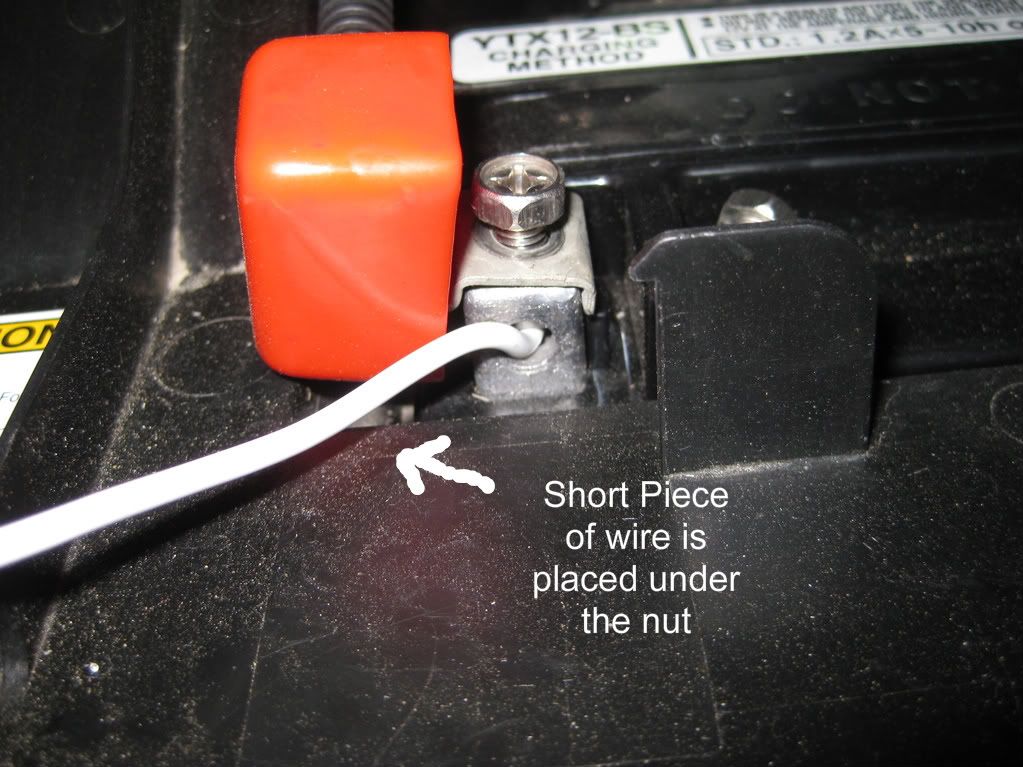
Take the in-line fuse that came with the driving lights and cut it off its wire leaving a few inches to either side. Then solder and heat shrink in about 10 inches of the red radio shack 12 gauge wire to one side of the fuse and about 5 ft of the red radio shack wire to the other side.
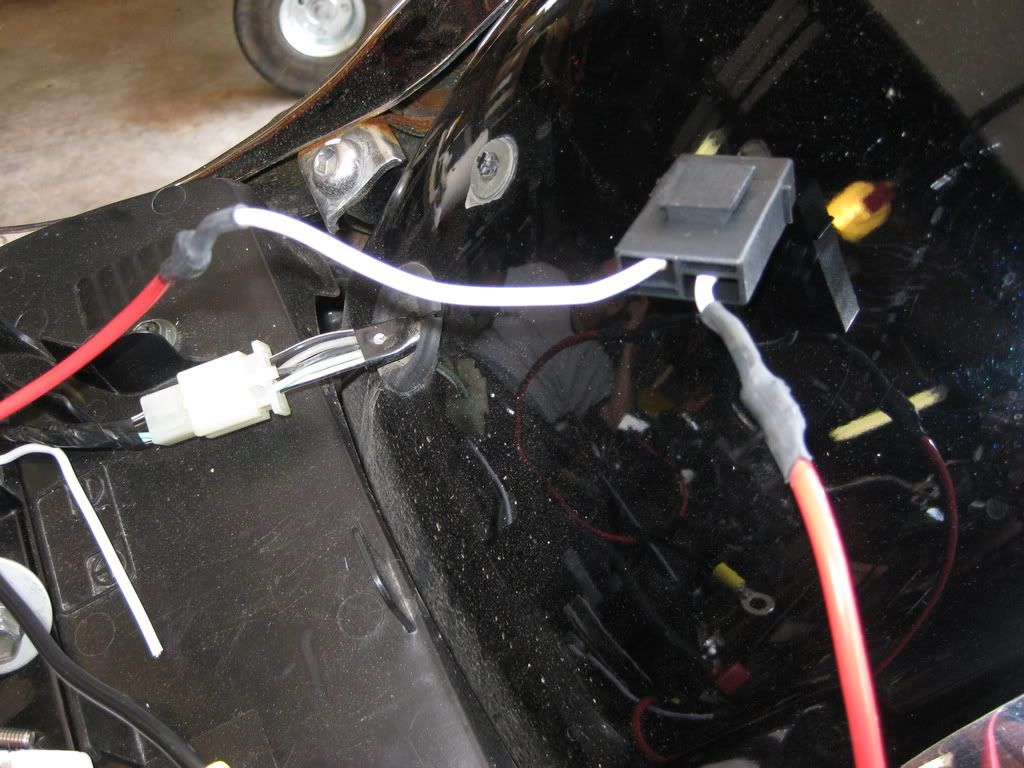
Next at the end of the 10” side Crimp then solder on a Battery connector.
Next take about 5 ft of the black wire and on one end crimp then solder another battery cable.
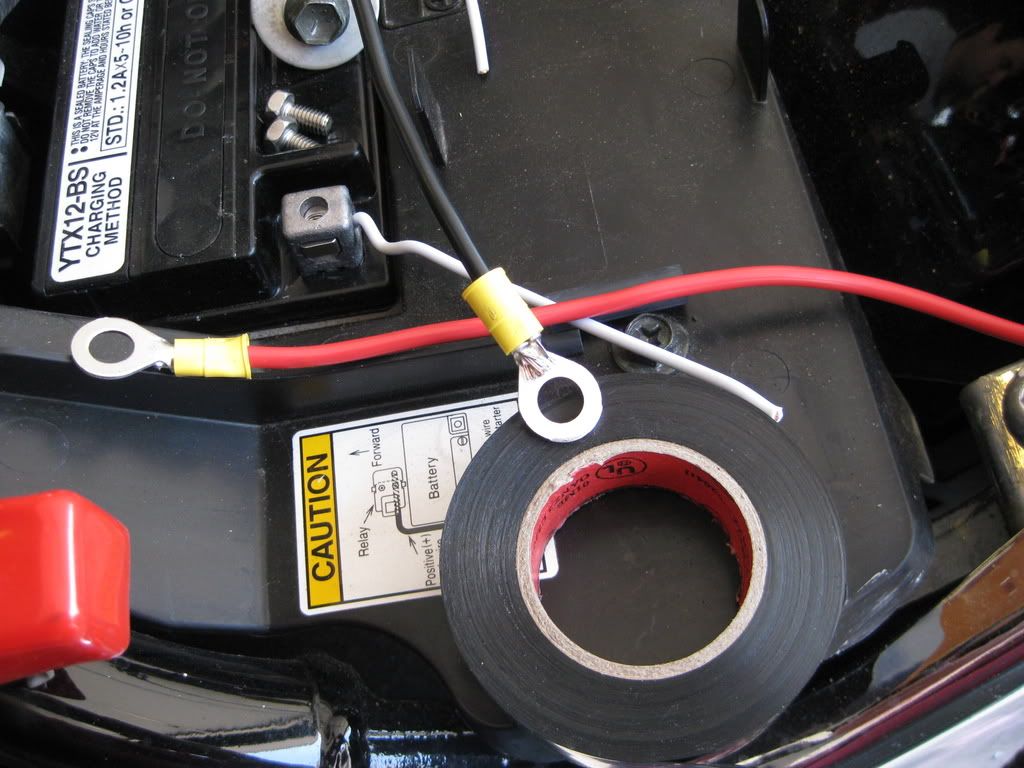
Do Not connect to the battery at this time….that will be the last thing that you do.
Your going to bind the red and black wires together every few inches with electrical tape and run it into the headlight bucket leaving enough of slack make all you connections. Secure the wires every few inches with wire ties where ever you see fit to secure it.
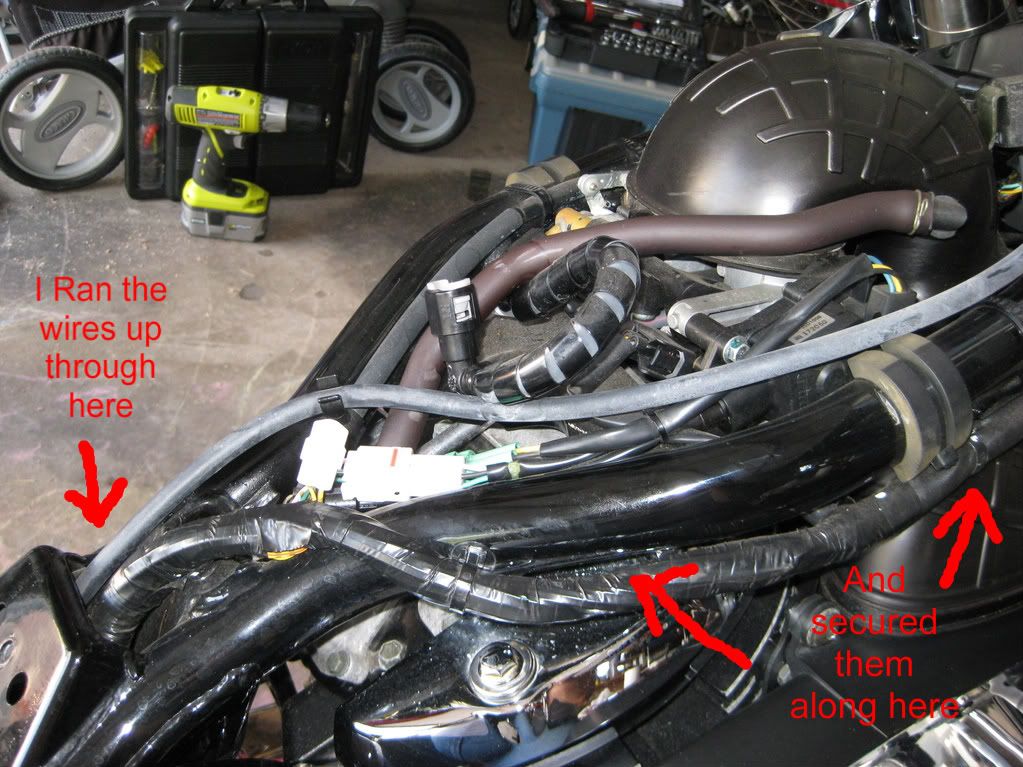

Then you can secure the tank back to the frame.
Open the Headlight Bucket.
Open the Pilot Relay Wiring Harness from the auto store. (if you don’t have this harness you can still follow this procedure by following the diagram below, the harness just makes it a little easier by making a plug for the relay)
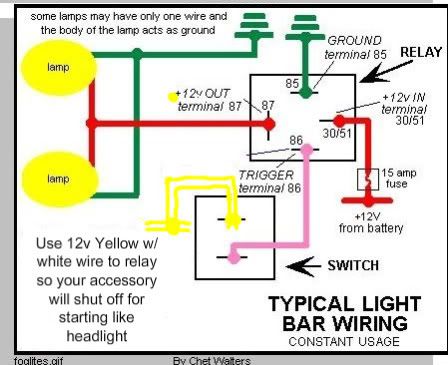
Locate the Yellow wiring harness in the headlight bucket and in that harness there is a yellow with white tracer wire that runs from the harness up the left side of the handlebar into the headlight switch. This wire will be the trigger wire for the relay. I chose to cut this wire and splice in the thin white from the PILOT RELAY WIRING HARNESS remembering to solder and heat shrink the connection. This is the wire that will go to your switch, (I don’t have a switch yet so for me this wire goes right to the relay harness) whether you put it into the speedo housing, or on the neck, or mounted on the handlebars. Now from the switch you will run another piece of 16 gauge wire to the trigger terminal on the relay housing which happens to be the thin white wire coming from the housing. If you are using a switch please either use spade terminals to connect to the switch or install a plug so that in the future you can completely remove the speedo housing.
If you are installing a switch into the speedo housing use a good quality switch like the one from Allied with an external rubber boot cover to keep it watertight. You can also use some Diaelectric compound on the inside terminals to further protect it, but that’s probably over kill.
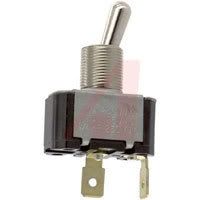
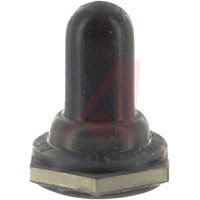
Also from the new relay housing are 2 larger gauge double white wires. These are the wires that will go to your lights. Connect the white wire from each light to the double white wire off of the relay housing in one soldered and heat shrunk connection. (tip: twist the white wire from each light together and then twist the two white wires from the relay housing together, and then twist the four wires together to form one large splice)
Connect our red wire from the battery to the large single white wire off from relay housing remembering to solder and heat shrink. This large white wire is the 12v in wire.
Connect the four remaining black wires together in a large soldered heat shrunk splice. The four black wires are: 1 each from the lights, the black main wire from the battery, and the ground wire from the relay housing.
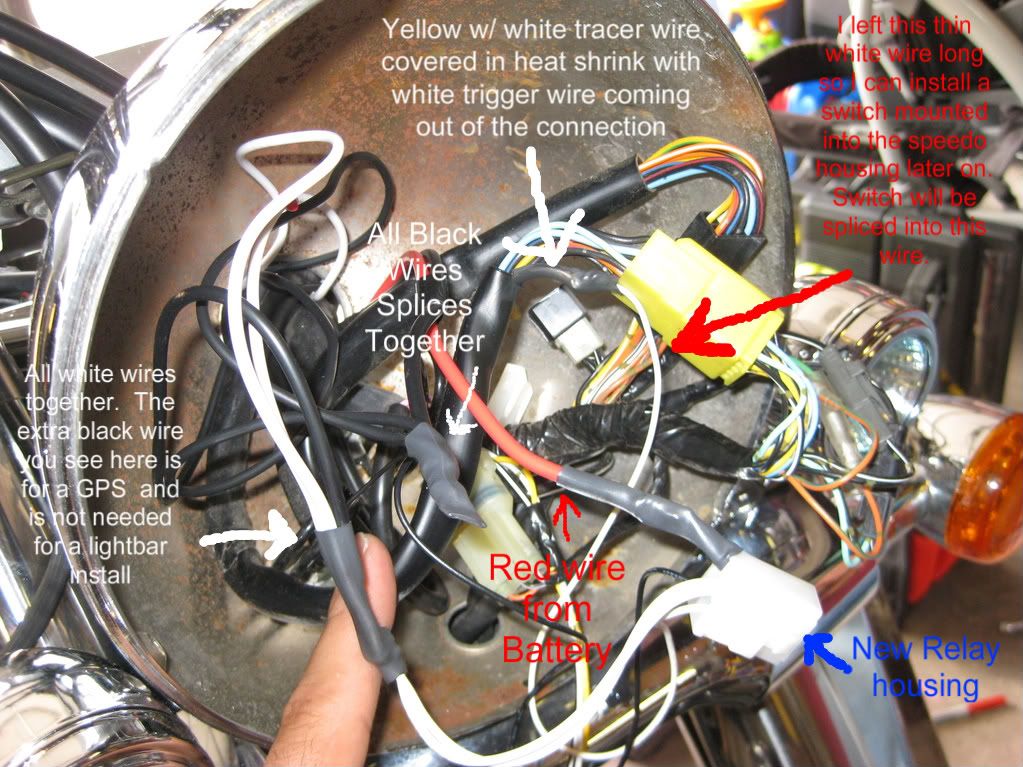
Now place all the wires neatly into the headlight bucket and affix the relay to the relay housing.
Clean up all of your exposed wires with the plastic wire cover.
Connect your Red and Black wires to the battery. (tip: remember to remove the little shots of wire holding up the battery nut) and your going to have to notch the flimsy red plastic casing that covers the red terminal to accommodate the new red wire. YOUR DONE!!!!
Now you are ready to test and button up everything.
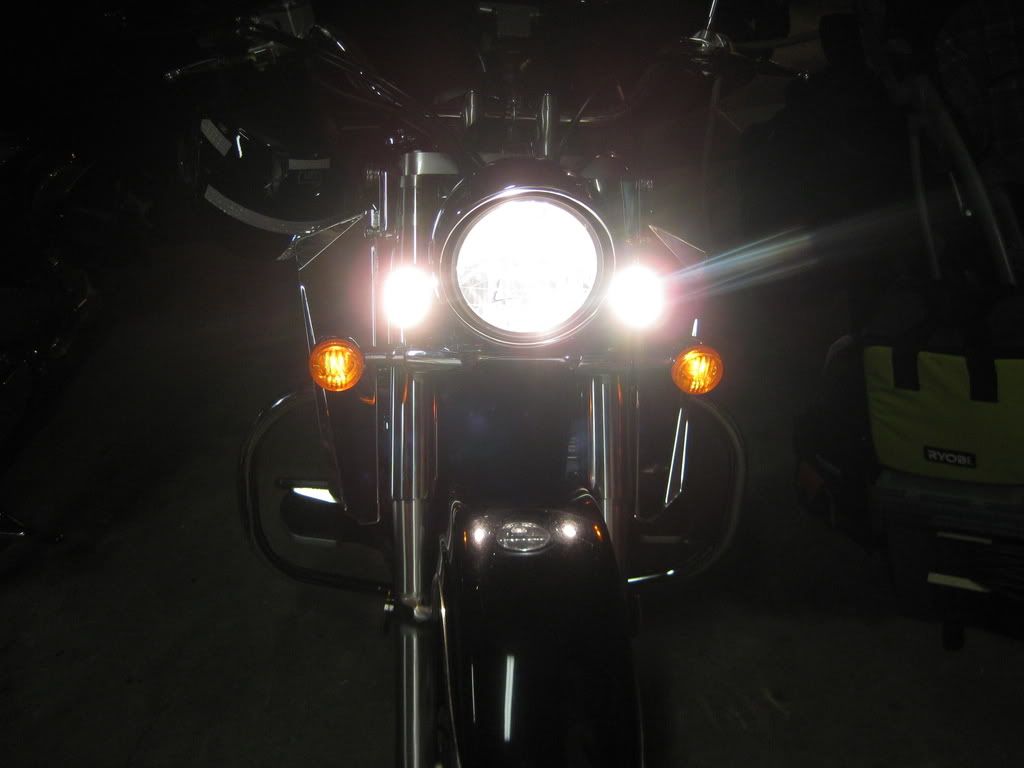
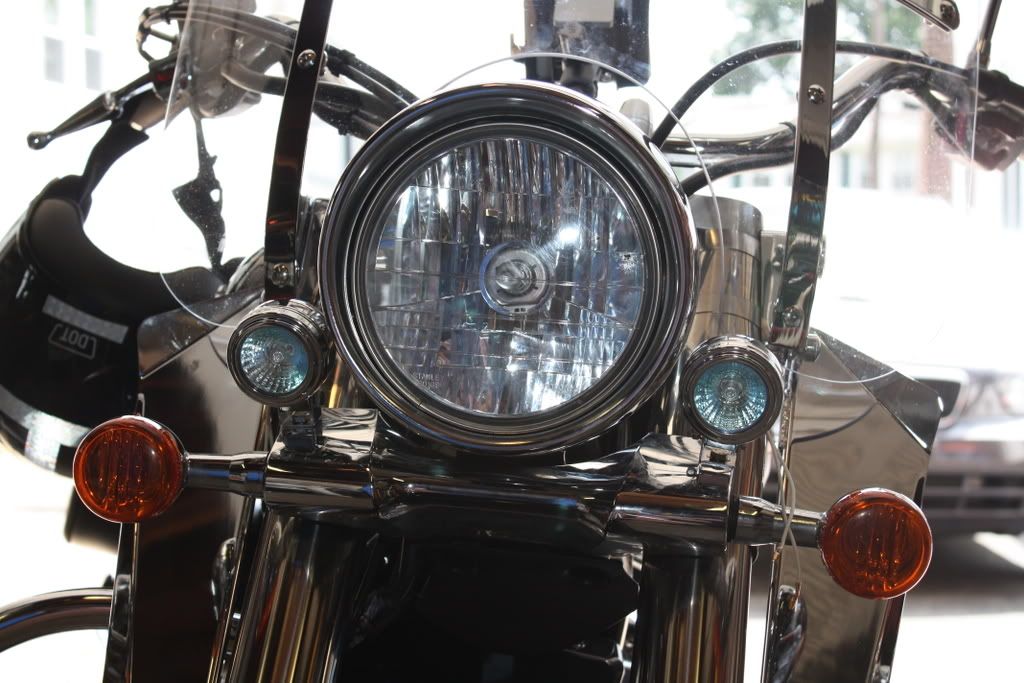
Good Luck!!!
James
Desert Dawg Chaps
For the colder weather I use Desert Dawg Chaps for the Cobra highway bars. They go on in about 10 minutes by just slipping them over the Cobra bars and then clipping them together. I can definitely feel some warmth behind them. I didn't notice any ill affects so far. These are fantastic!
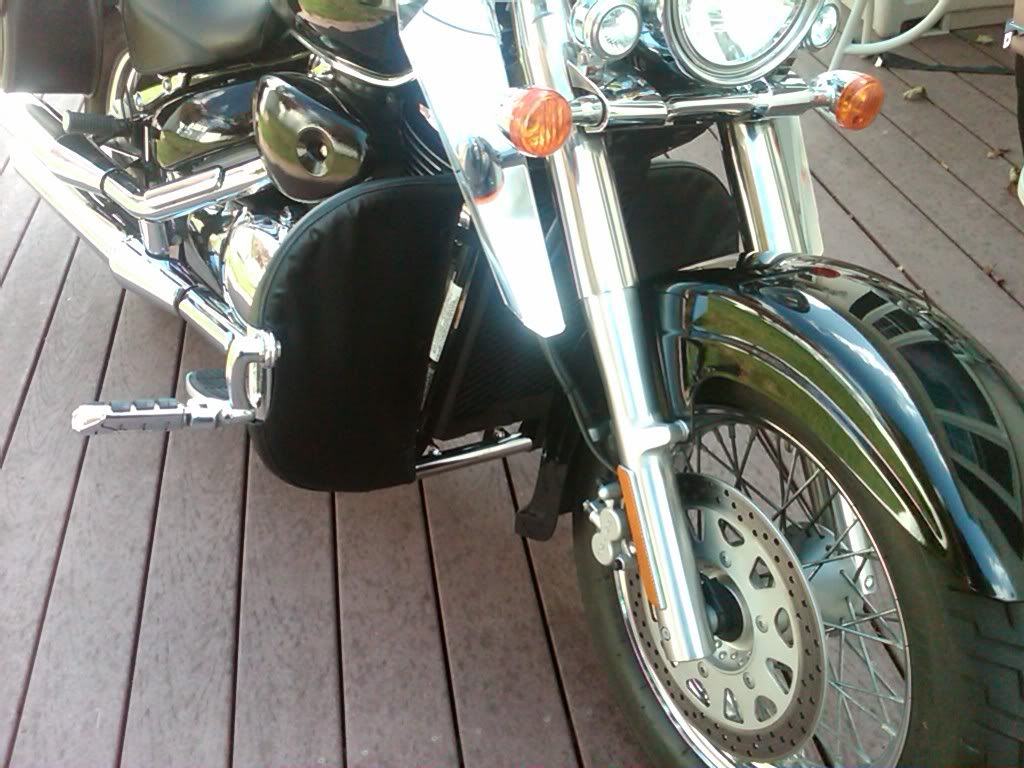
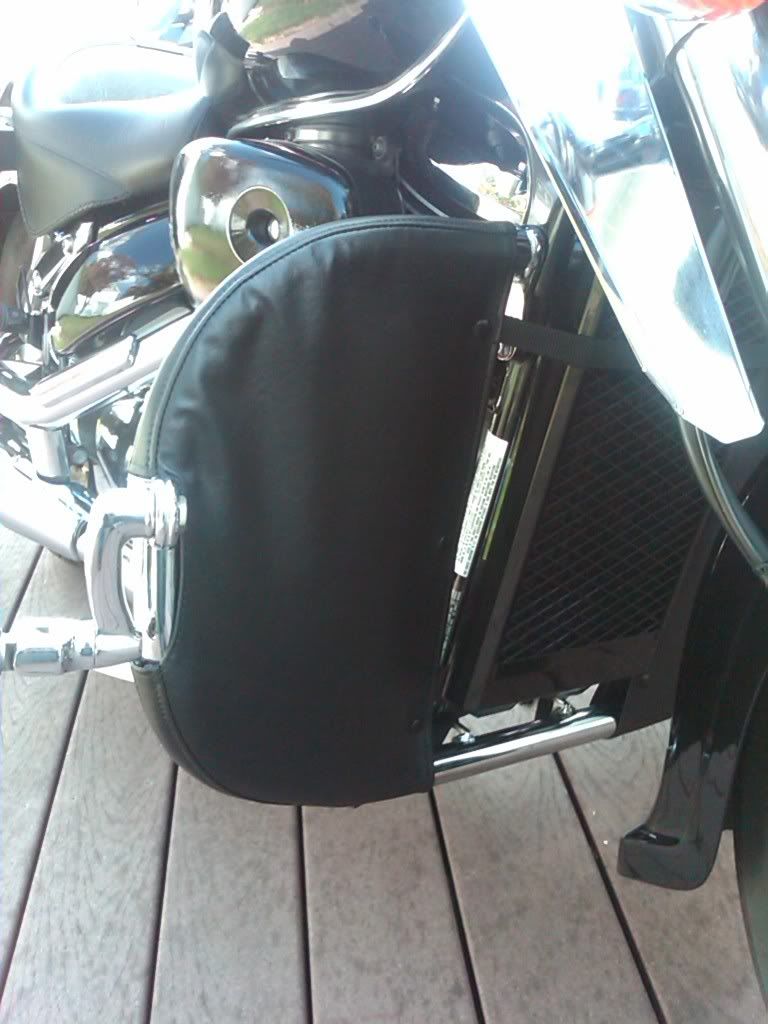

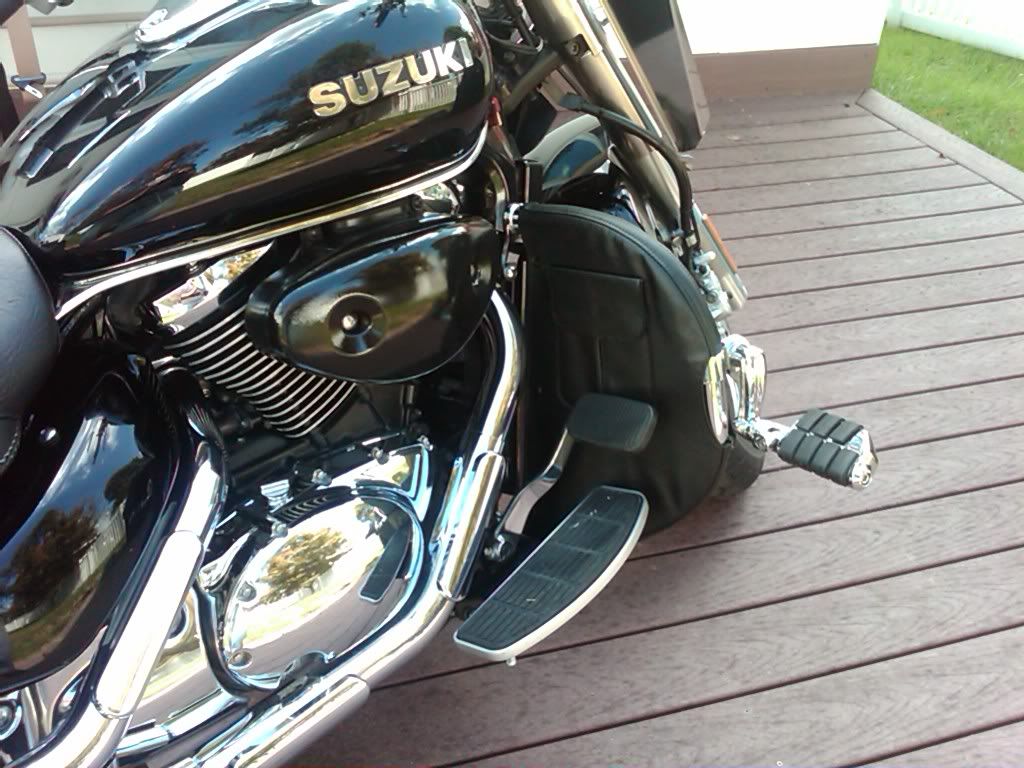
James
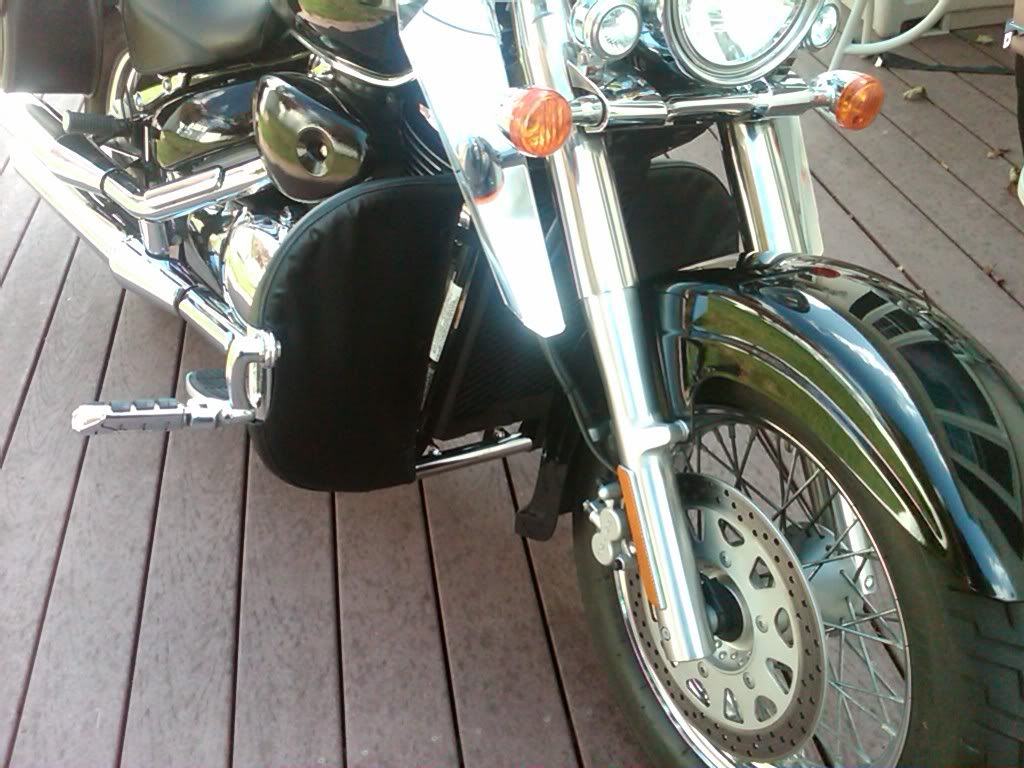
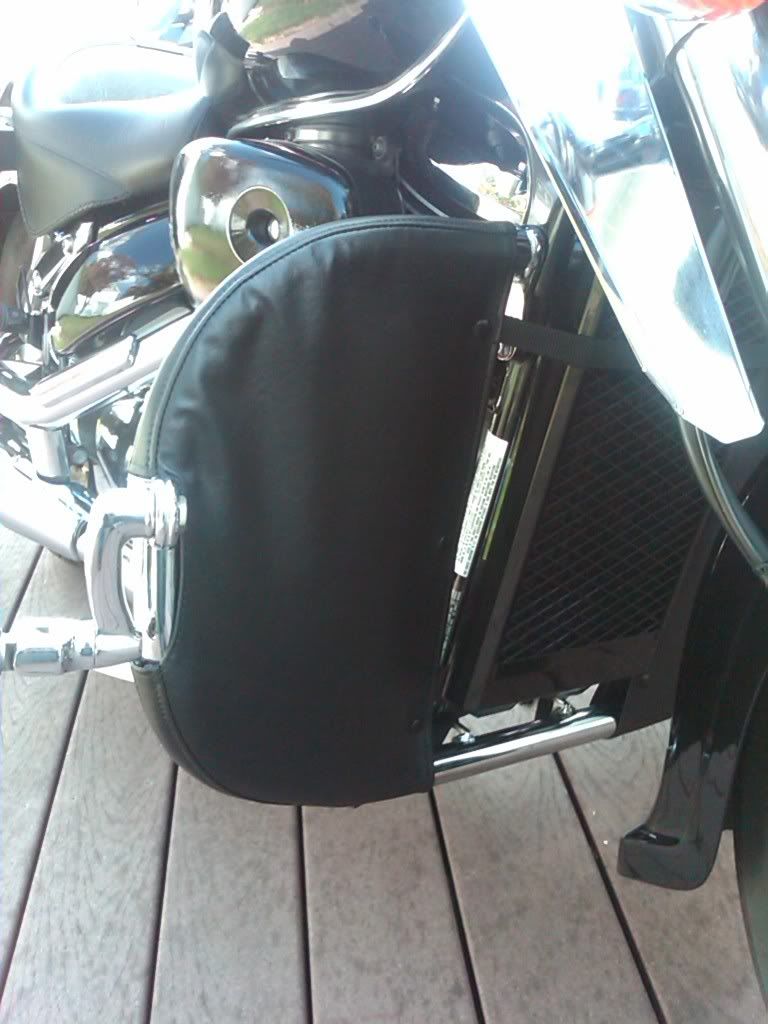

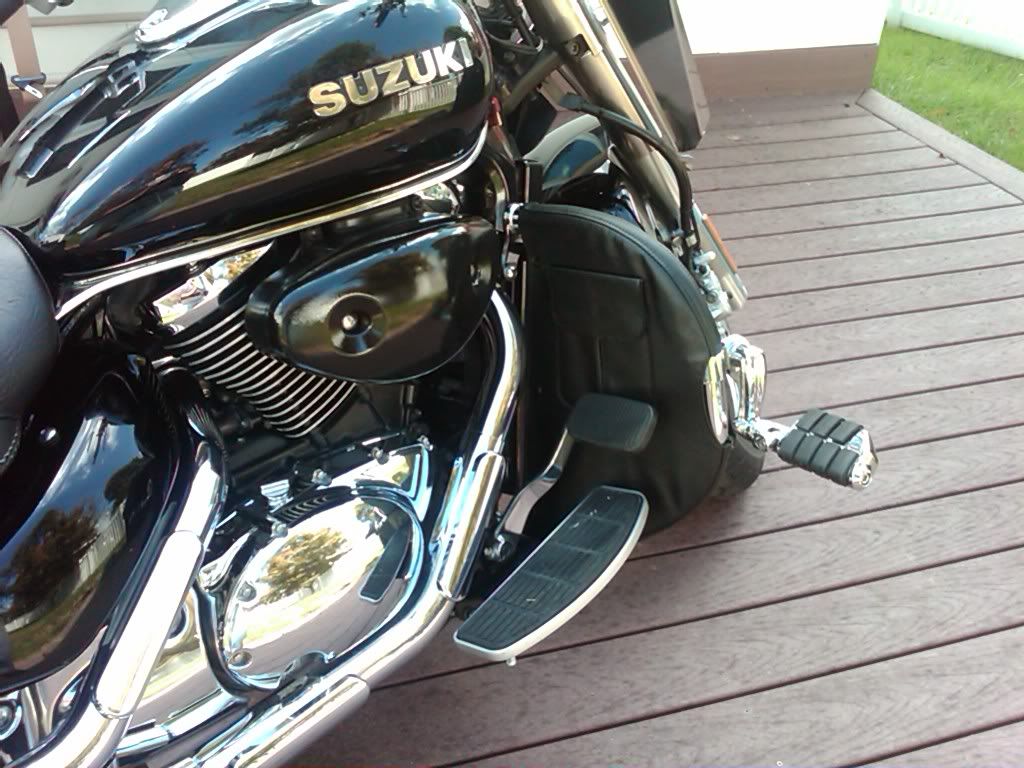
James
Progressive Springs
I felt that the Suzuki C50 was a diving to much in the front under braking so I changed the front springs out to Progressives. I used Progressive part number 11-1126. Since Progressive doesn't make spring specifically for the C50 I had to use the next best. These springs are about 5 inches to short so I had to cut some PVC pipe to fit. The combined length of the spring and spacer is 21.73", the length of the original spring. You should also measure the original spring and see if is still in spec. If it's less then 21.29" then it need to be replaced anyway.
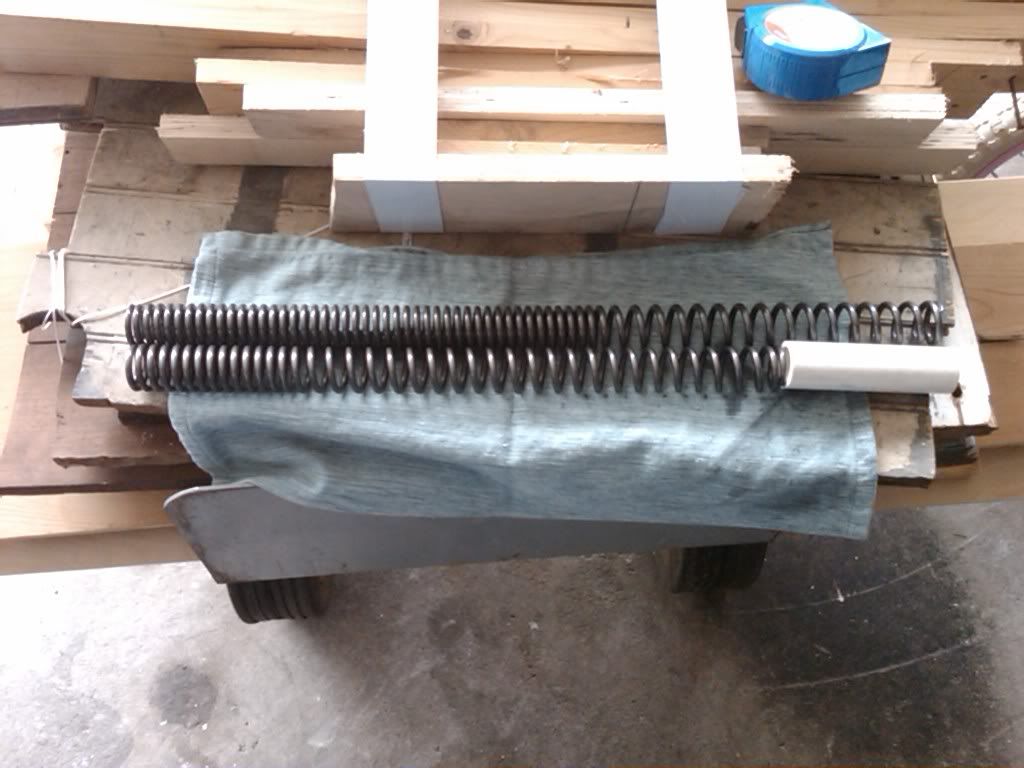
If you have risers then this might be an easier install because the springs might just be able to lifted out past the handlebars, but with the stock risers you will need to move the handlebars out of the way.
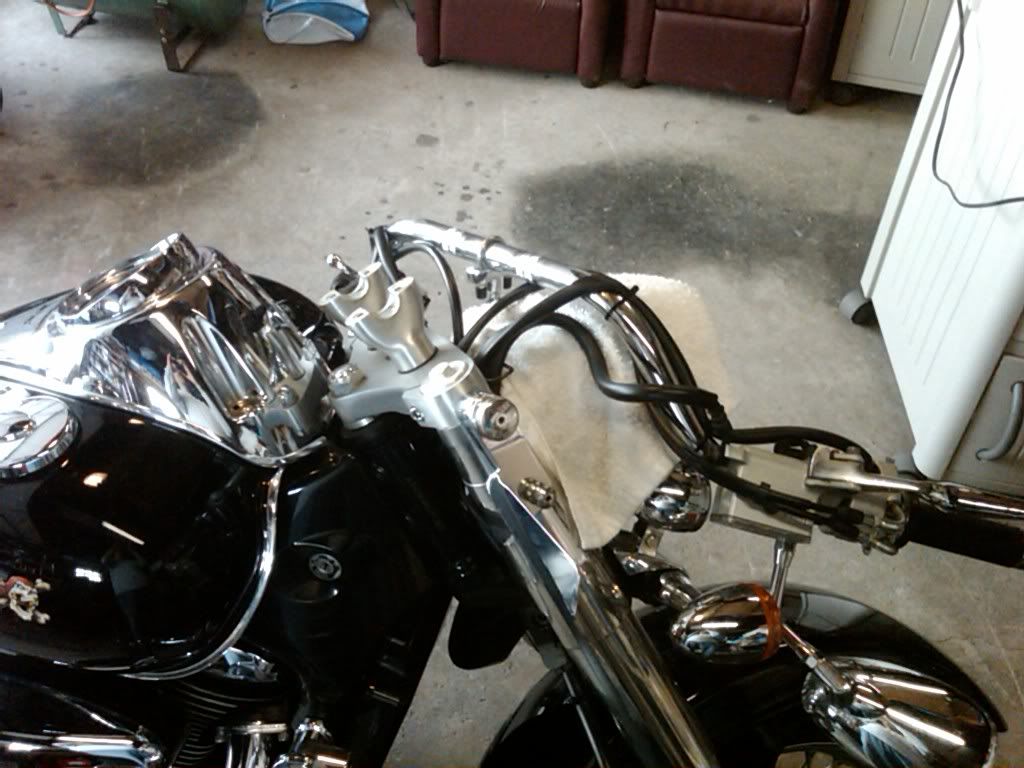
With the bars out of the way it's time to open the fork tube caps. You have to loosed the upper pinch bolt on the side of the triple tree first. Then comes the tube cap. Caution, the cap is under spring tension. You must have the bike on a lift and the wheel just off the ground to open this cap. Even with the wheel off the ground the cap is still under tension, just not as much. We came up with a method of removing these caps. We used a ratcheting box wrench and a dowel that fits inside it to counter the spring.
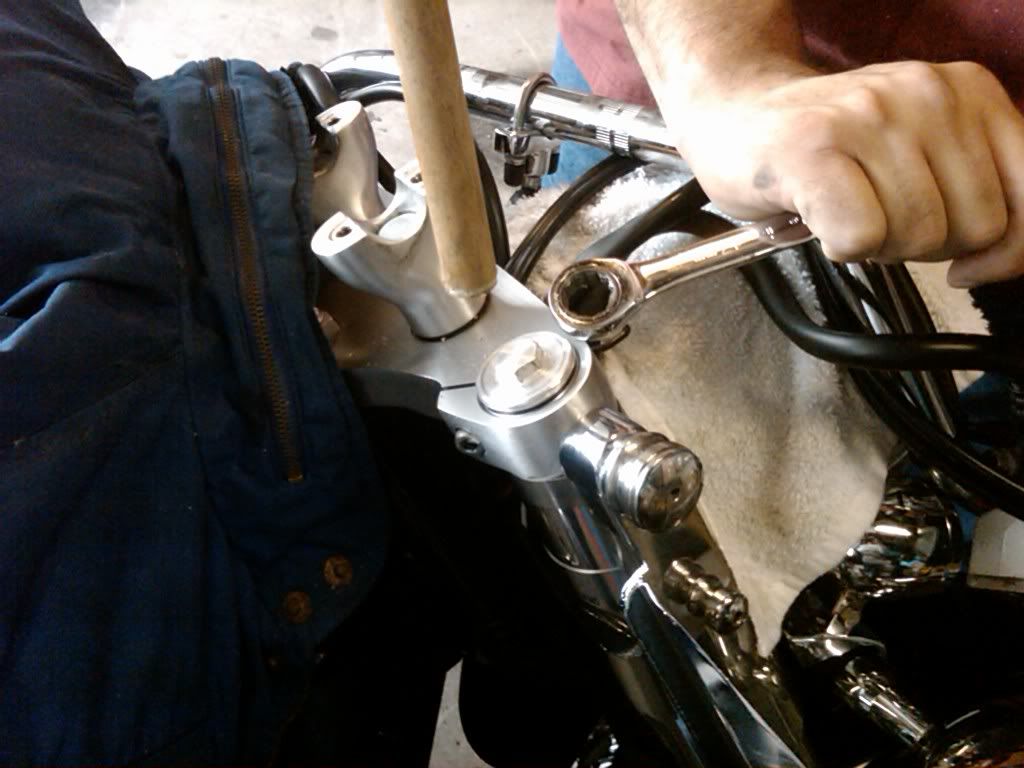
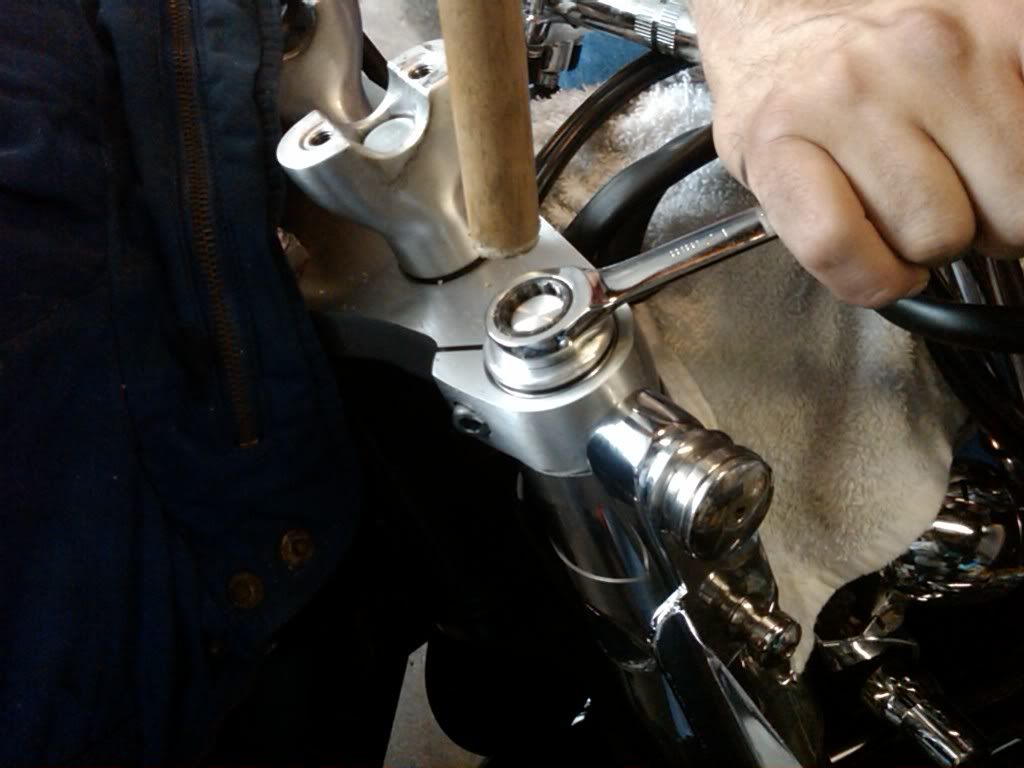
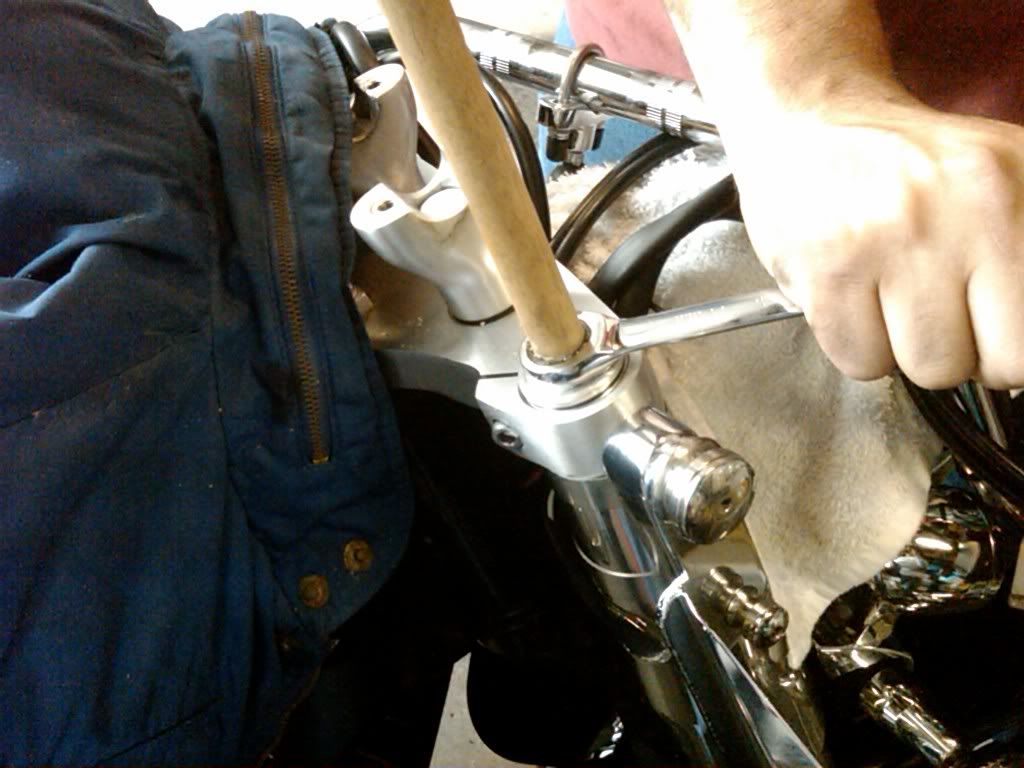
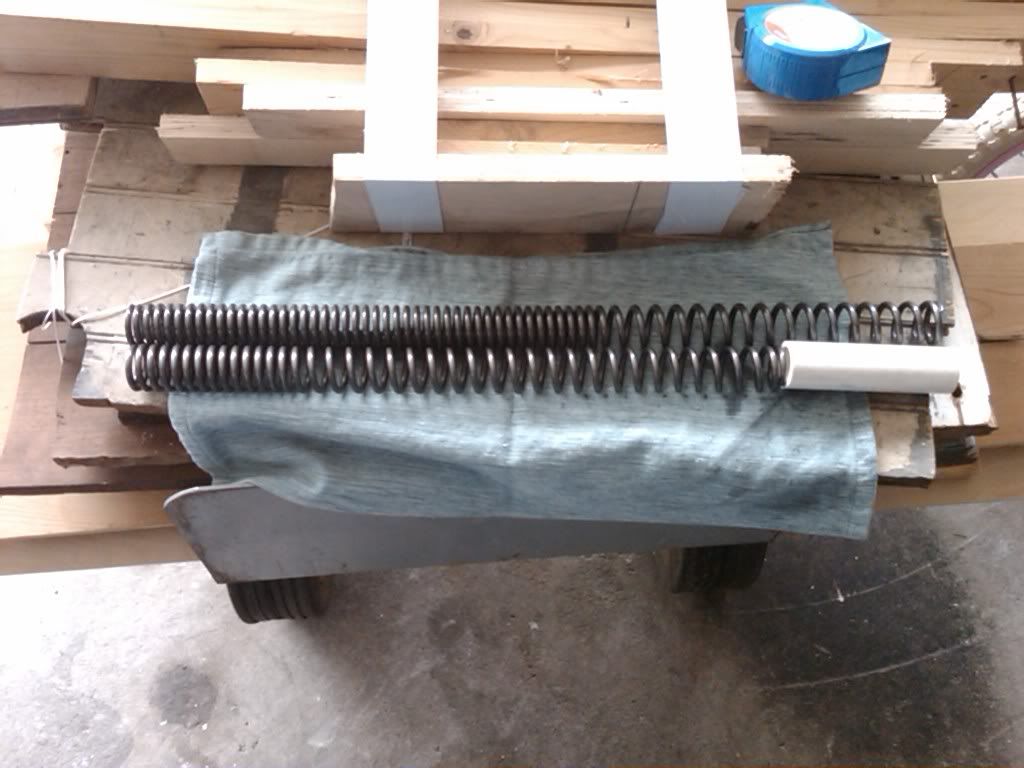
If you have risers then this might be an easier install because the springs might just be able to lifted out past the handlebars, but with the stock risers you will need to move the handlebars out of the way.
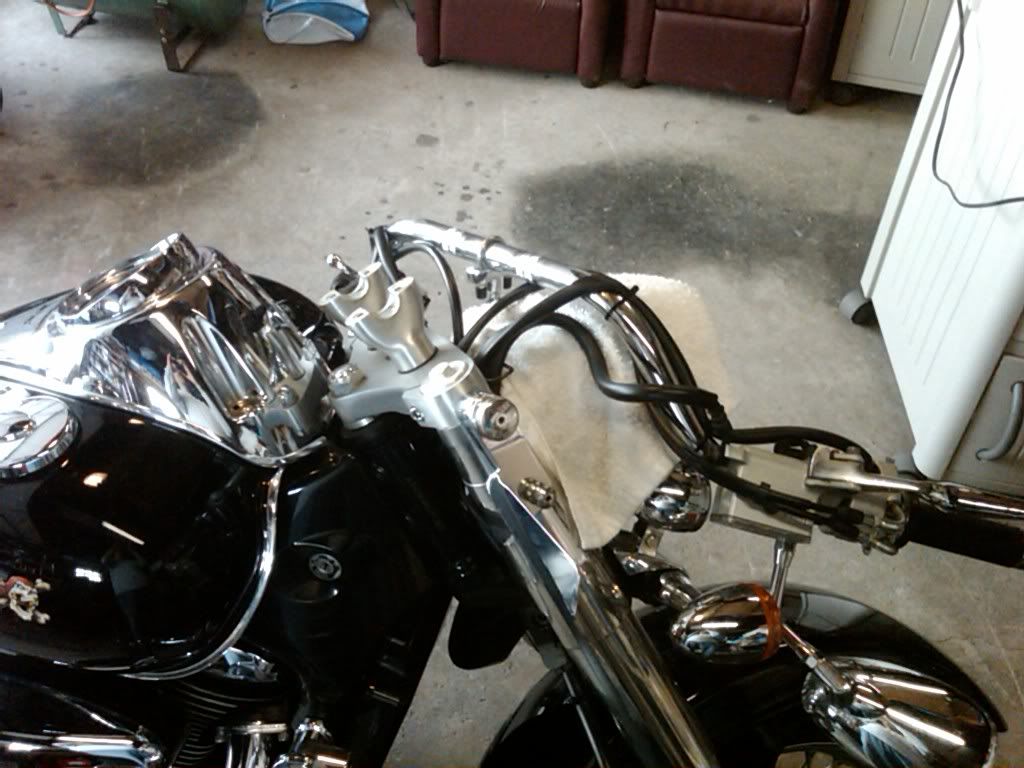
With the bars out of the way it's time to open the fork tube caps. You have to loosed the upper pinch bolt on the side of the triple tree first. Then comes the tube cap. Caution, the cap is under spring tension. You must have the bike on a lift and the wheel just off the ground to open this cap. Even with the wheel off the ground the cap is still under tension, just not as much. We came up with a method of removing these caps. We used a ratcheting box wrench and a dowel that fits inside it to counter the spring.
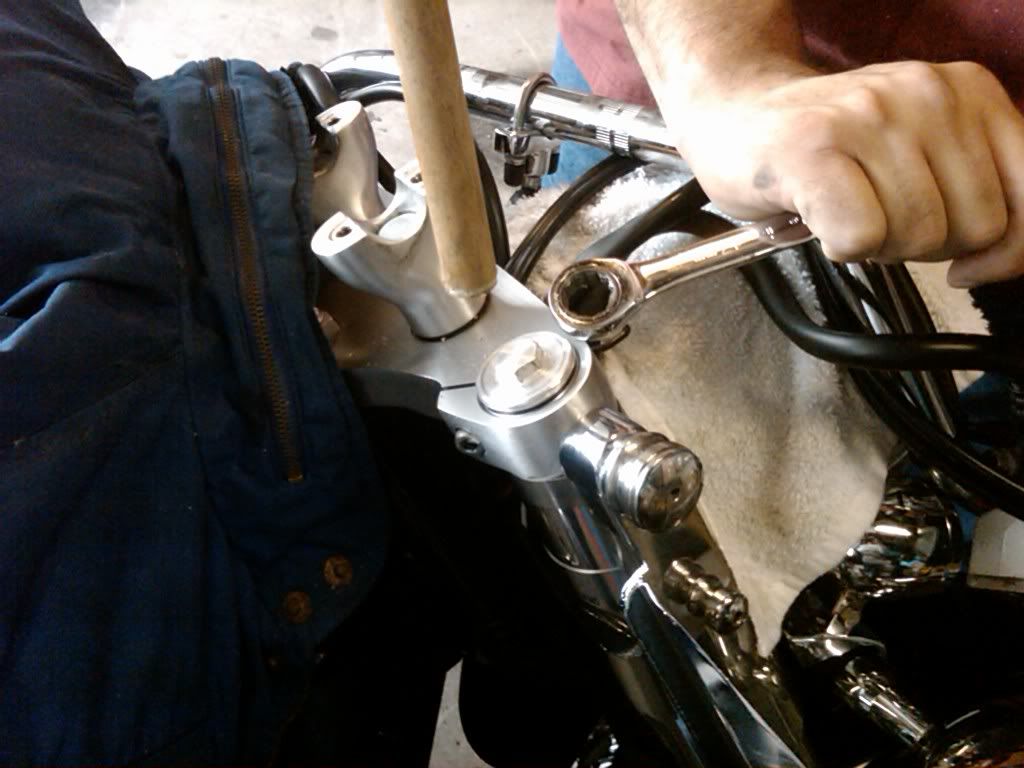
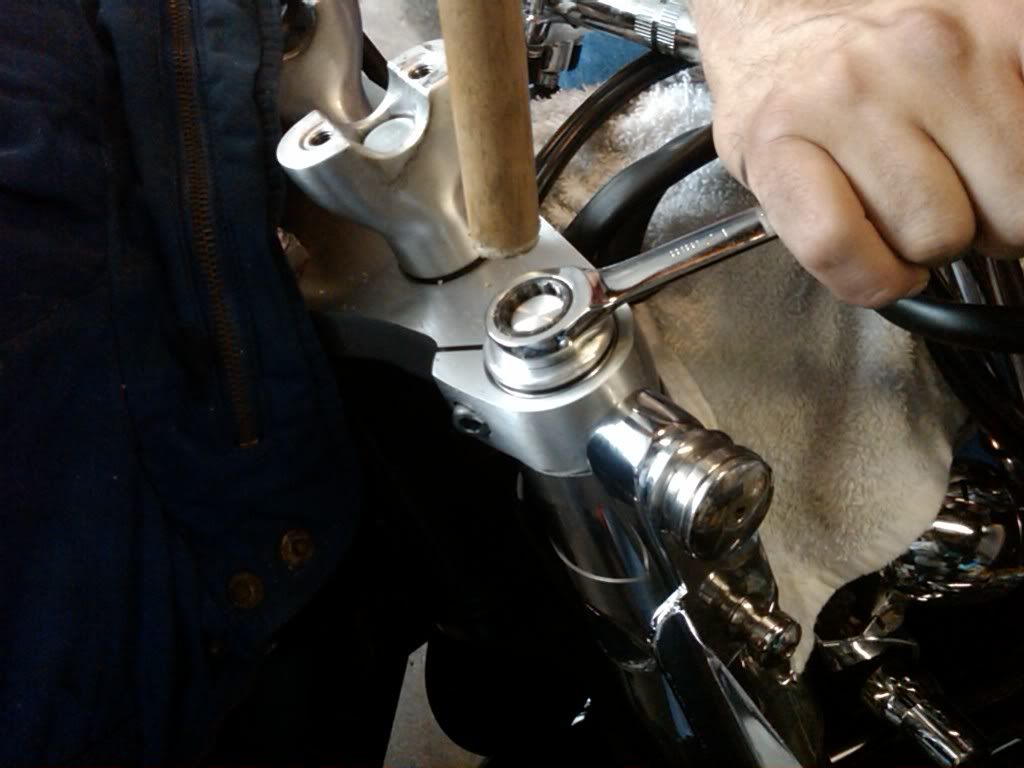
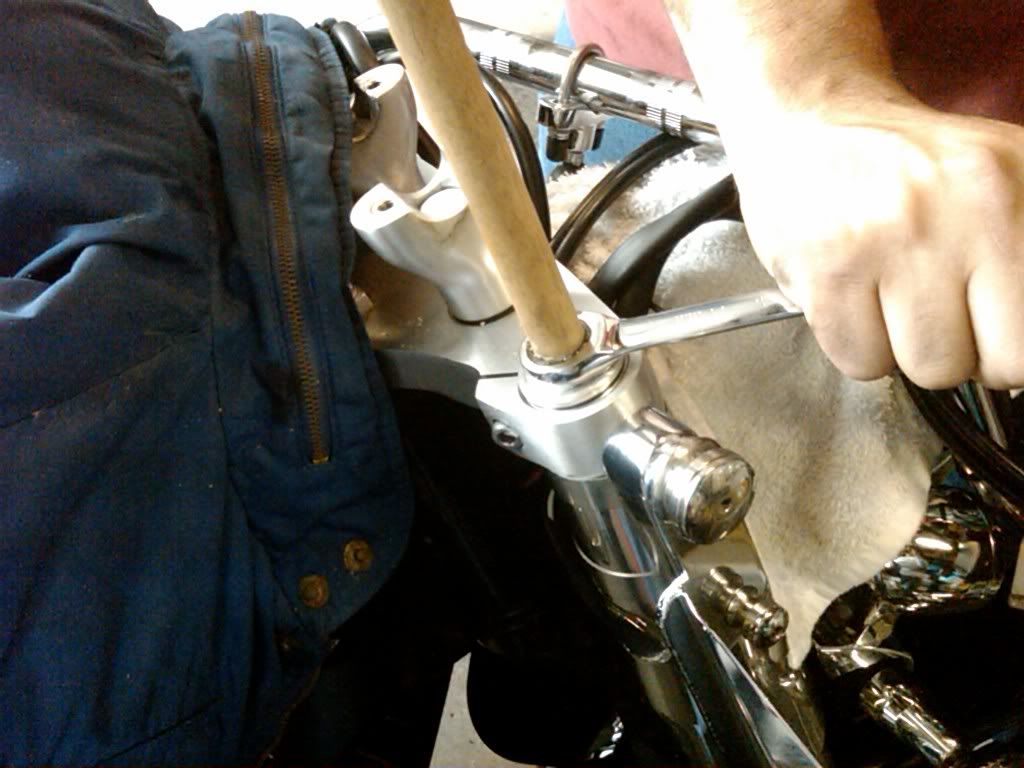
Since then we learned that we didn't need the dowel because we became accustomed to the amount tension that is under that cap. There is a lot of threads on that cap, so when you get to the end just keep a rag over the cap and place you other hand over the rag, pressing down, to catch the cap when it POPS off. If you don't cover it, it will shoot up to the top of the garage or it can hurt someone, please take precautions here.
When I first opened the riser tubes I noticed that the fork oil level was way low, they should be 6.96" measured from the top of the tube to the oil without the springs in and the forks collapsed. Also, the capacity of each fork tube is 412ml or 13.9oz, so if you were to remove each tube and turn the tube over to drain out the oil, then you can just add that amount back. I think that most of us should at least check the oil level because low fork oil level would definitely add to the front end diving under braking.
Remember to torque the top cap and the pinch bolt to the right setting when you reinstall. Cap bolt should be 25.5 lb-ft and the pinch bolt should be 16.5 lb-ft
Now I have the Progressives in, and the oil level set to the proper level. I can say that there is a remarkable difference in the ride. Handling and braking feels great.
If you folks take anything away from this write-up then it should be to check the oil level. If you siphon out the old oil and replace with new oil set to the proper level you should see a big difference in your ride.
This is a link to the oil level adjusting tool I used. Something else for the motorcycle tool box.
__________________
When I first opened the riser tubes I noticed that the fork oil level was way low, they should be 6.96" measured from the top of the tube to the oil without the springs in and the forks collapsed. Also, the capacity of each fork tube is 412ml or 13.9oz, so if you were to remove each tube and turn the tube over to drain out the oil, then you can just add that amount back. I think that most of us should at least check the oil level because low fork oil level would definitely add to the front end diving under braking.
Remember to torque the top cap and the pinch bolt to the right setting when you reinstall. Cap bolt should be 25.5 lb-ft and the pinch bolt should be 16.5 lb-ft
Now I have the Progressives in, and the oil level set to the proper level. I can say that there is a remarkable difference in the ride. Handling and braking feels great.
If you folks take anything away from this write-up then it should be to check the oil level. If you siphon out the old oil and replace with new oil set to the proper level you should see a big difference in your ride.
This is a link to the oil level adjusting tool I used. Something else for the motorcycle tool box.
Kurkakyn 5001 Constellation Light Bar
Meet the Kuryakyn Constellation Light Bar, part 5001. It is a three piece light bar that is adjustable front and back, for width, and angle to the ground. It uses an H3 bulb for the driving lights and standard turn signal bulbs.
Once you remove the plastic turn signal cover plate, you then remove the turn signal bracket along with the old signals. Disconnect everything inside the light bucket. Then you install the Kuryakyn mounting bracket (4006) under the lower triple tree that the light bar mounts to.
What I like about this light bar is that it has a very CVO look to it.
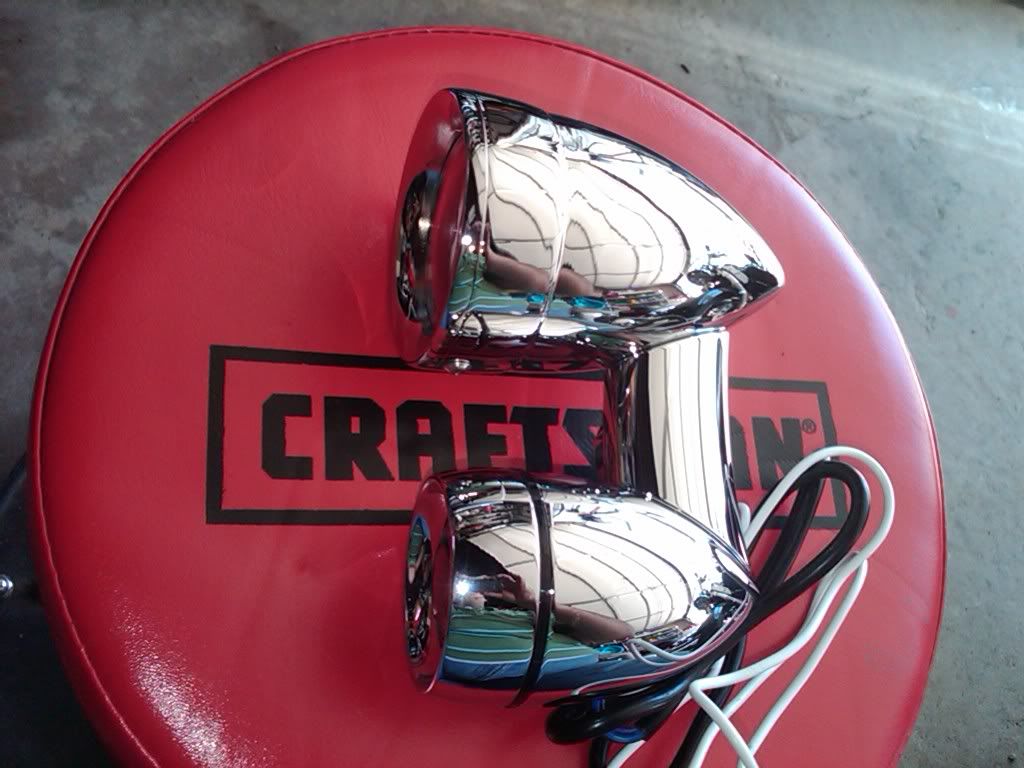
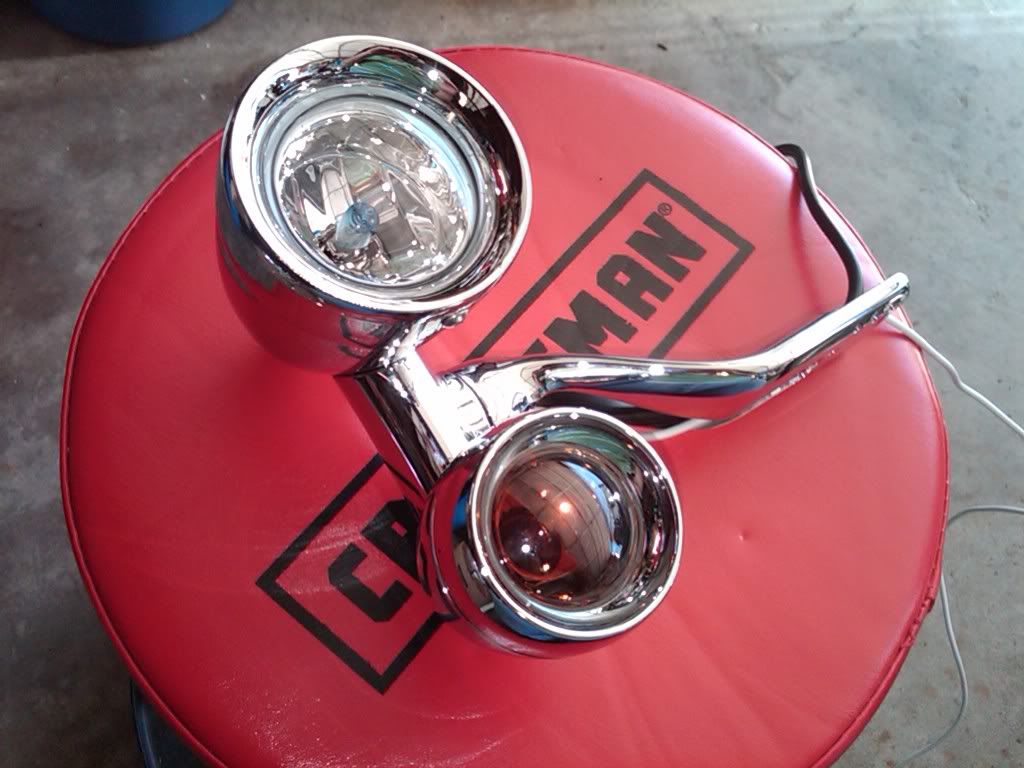

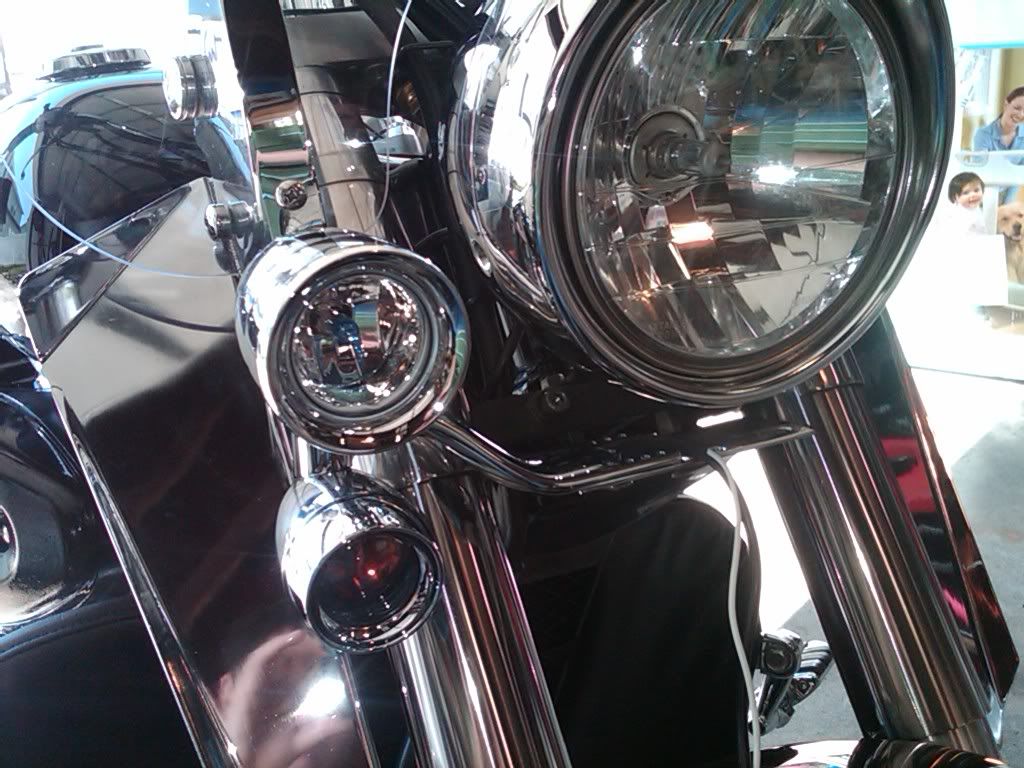


Once you remove the plastic turn signal cover plate, you then remove the turn signal bracket along with the old signals. Disconnect everything inside the light bucket. Then you install the Kuryakyn mounting bracket (4006) under the lower triple tree that the light bar mounts to.
What I like about this light bar is that it has a very CVO look to it.
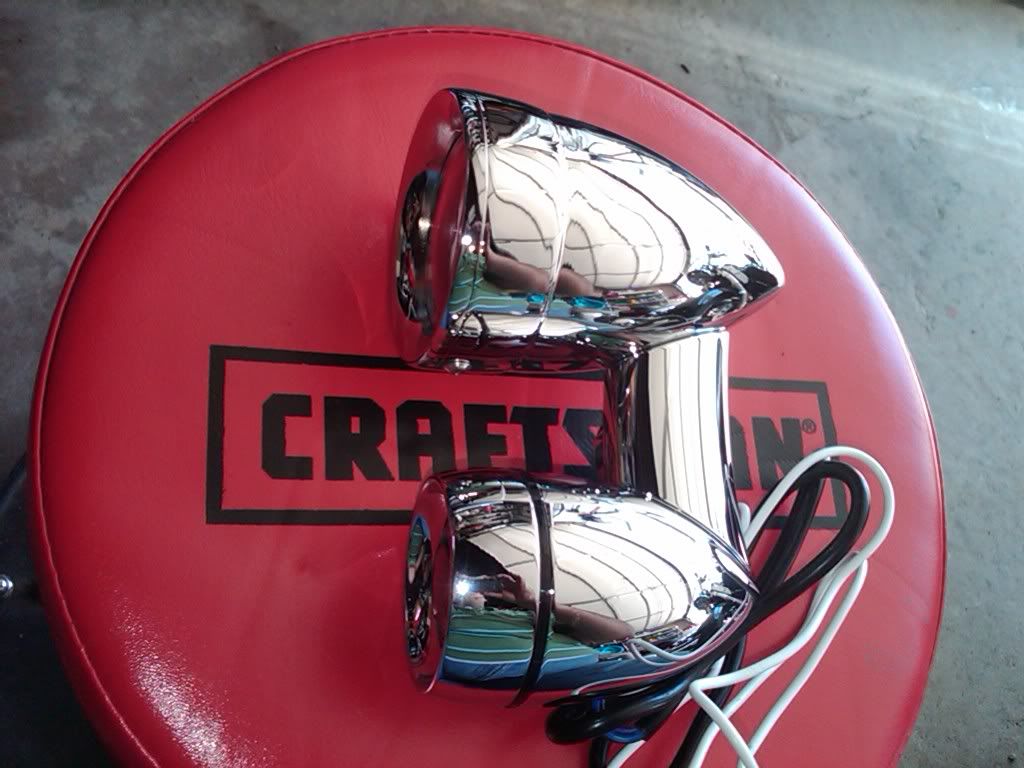
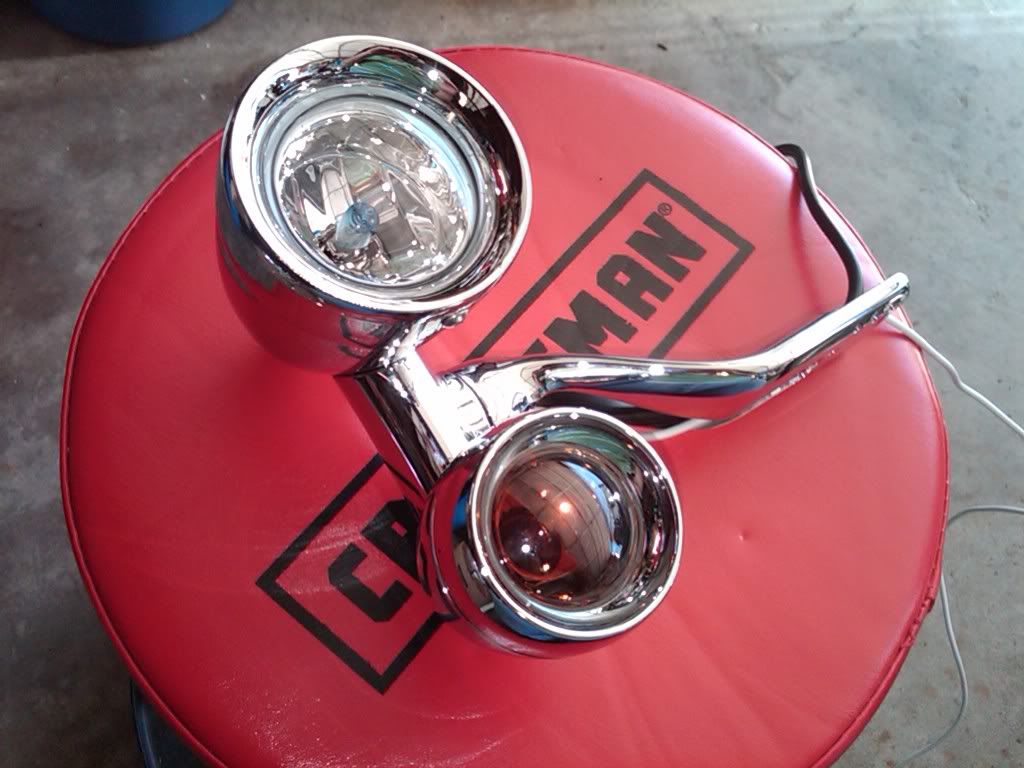

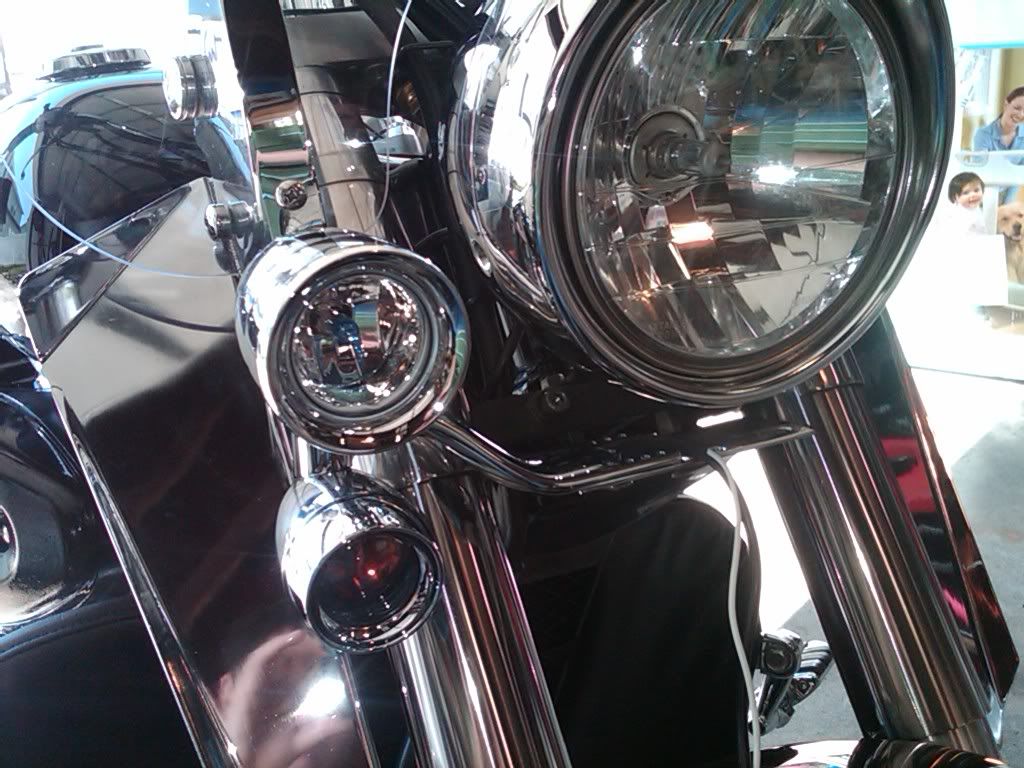


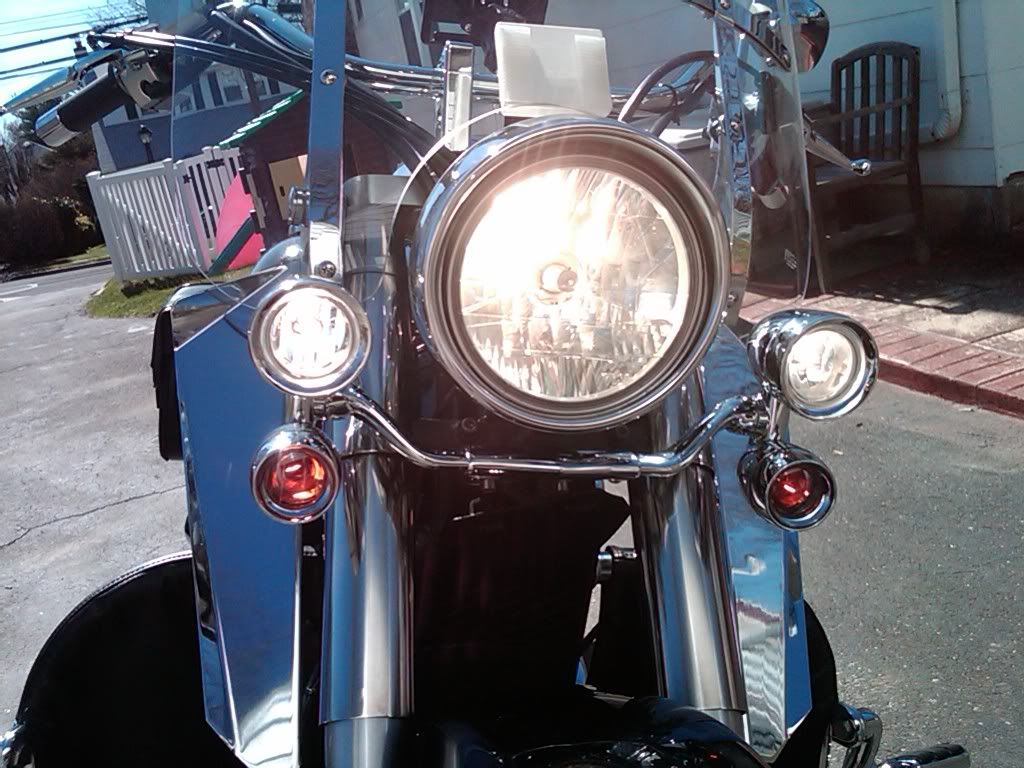
I replaced the smoke turn signal lens seen here with Kurkaykn's amber lens and I am more satisfied with the color of the turn signals now. With the smoke lens they seemed a little dull.
Subscribe to:
Posts (Atom)